(* I was not easily able to get a total count. Peirce's 'Swords of the Viking Age' states "Some thirty to forty examples with the name Uflberht are known in Finland". Since that is some distance from the FranKish origin of the blades, and also only a small portion of the active Viking Age, the total number in existence must me quite large.)
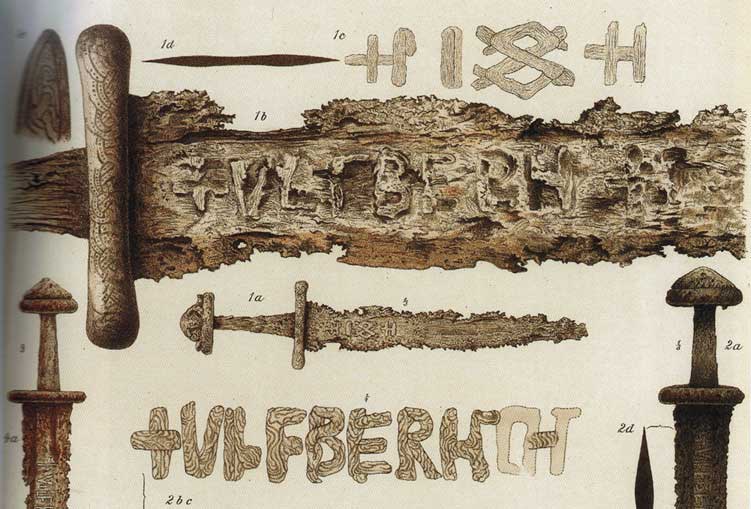
Uflberht swords all have that makers name inlaid into the blade. The rough forged blade was engraved to create a channel. Into this channel was inlaid strips of metal. In a number of cases, this inlay was made of pattern welded material. The channels were undercut, allowing cold hammering of the inlay material to lock it into place. Then the blades were heated, and the inlays forge welded into place. After polishing, the difference between the metal of the body of the blade and this inlay would be subtly visible.
Image(right) taken from 'Swords of the Viking Age' by Ian Peirce - original caption:
'Examples from the collection of Bergens Museum, Norway of +ULFBERHT+ twisted laminated rod iron inlaid inscriptions ... Plate 1 from A.. Lorange, Den Yngre Jernalder Svaed (Bergen 1889)'
I had been contacted by Elizabeth Ward, who I had worked with on Vikings, North Atlantic saga, back in December. She was now working on a new exhibit for the National Museum in Iceland. (A project which got completely fouled up by the Credit Crunch and problems with the major banks in Iceland.)
One of the objects she was potentially interested in having reproduced was an 'Uflberht' sword. I certainly have never attempted this method! On the advice of my friend Neil Peterson, I contacted a couple of other smiths who have much better experience in sword making than I do. ( This on the assumption that I do no damage to my own reputation by knowing when its time to recommend others with higher skills than my own!)
Jake Powning is another Canadian, I met him at CANIRON 5 when I was demonstrating VA iron smelting there.
Jake's work is truly amazing. Normally he produces blades one at a time, not on commission. He personally said he had never done the pattern weld inlay technique seen on the original Uflberht blades. He called me and we pushed this around for about an hour. We both had similar ideas on just how you might accomplish this using historic methods.
He recommended yet another fellow - Jeff Pringle out of California (who unfortunately does not have a web site). He has actually done a number of Uflberht blades using correct methods. You can see an image on Bill Short's web site on VA swords (very good information there - Bill works with the Higgins Armoury Museum)
Near the top is a sword with the inlay copper and silver, down near the bottom is the correct Ulfberht method of welded strips on an iron core.
Jeff wrote me a short description of how he does this, along with the images below. He said
"The welding on an Ulfberht is easier than on a multi-bar composite sword, the difficulty is in the precise forging needed to make the inlay come out correctly on the finished sword..."(Maybe easy for YOU, Jeff!)
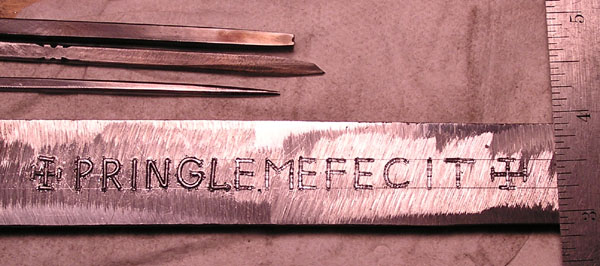
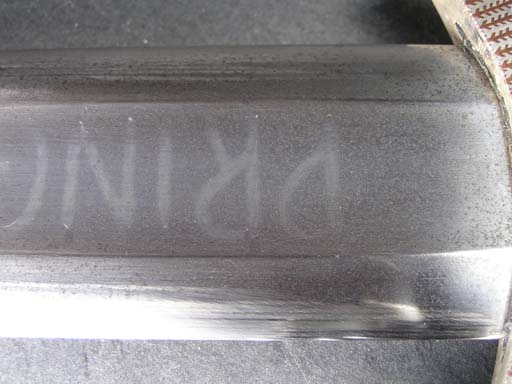
Knowing I was well out of my own skill depth, I considered how I might create a similar effect to the historic engrave, inlay and weld method:
First I forged out a billet from some of the good quality 'Ohio Bridge' wrought iron I have stockpiled. This material all from the same bridge, originally built in Ohio about 1860. It is wonderful material, well consolidated and relatively clear of slag inclusions. It does display an wonderful texture when surface etched. The starting billet was about 6 1/2 " long by 1 1/4 " wide by 5/16 " thick.
On to this surface I laid on some lines of mild steel using my small MIG welder. I tried to keep the patterns as straight and clean as I could, building up a bead about 3/16 inch above the surface.
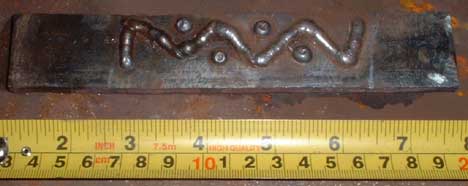
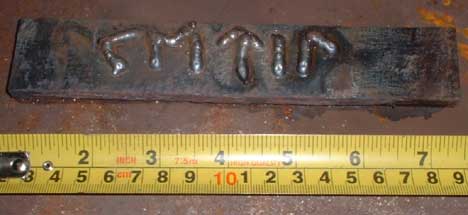
Next I hammered the billet flat, compressing the raised lines to flush with the surface. In retrospect, this might not have been the ideal way to proceed. The mild steel and the underlaying wrought iron have different hardness. The raised figures did compress and spread, but also collapsed the softer iron underneath them. This resulted in significant gaps along the edges of the figures, which showed as cracks in the billet surface. The slight difference in oxidation rates between the two metals shows in the images below:
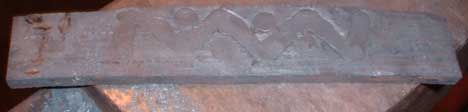
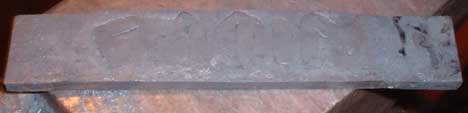
Once I had a flattened billet, I forged it into a large seax blade.
The cracks around the edges of the patterns came back to haunt me during the polishing stage. The blade was shaped to the classic Norse V grind, which alone generally means more polishing work to get to the final profile. I ended up taking a lot of material off both sides in an attempt to remove all those cracks.
The finished blade is 8 inches long, 1 1/4 " wide at the tang end and 1 1/2 at the start of the diagonal clip to the slightly raised point, and 3/16 thick at the back. Polishing was at 80 grit, and the finished blade was lightly etched in ferric chloride.
The images below are direct scans, reduced to grey scale. (click for the enlarged versions)
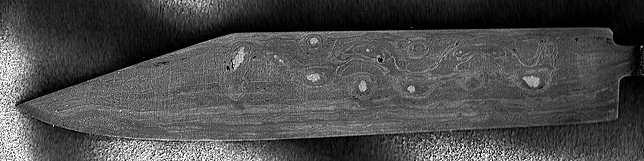
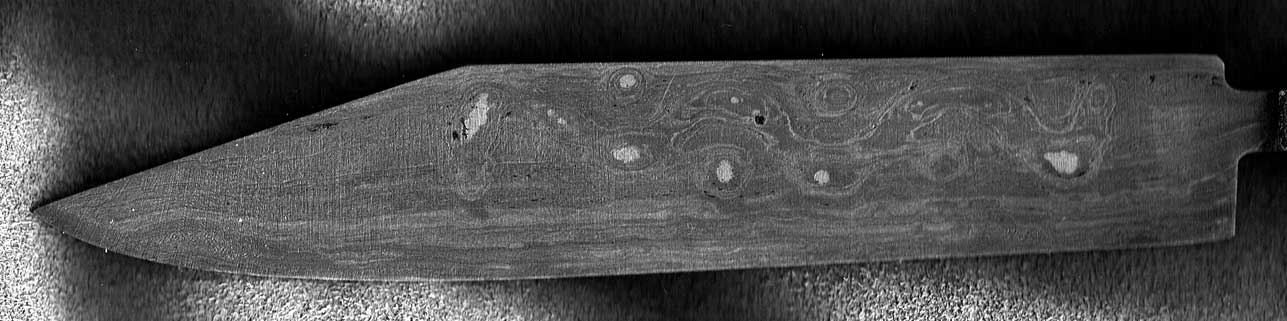
On this side you can see that most of the flaws have been ground away. This also has removed almost all of the mild steel deposit. The pattern is still visible from the compression of the wrought iron, resulting in distortions of the linear texture of that base material. The mild steel shows as light grey patches, mainly on the dots.
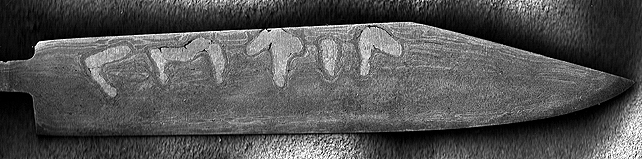
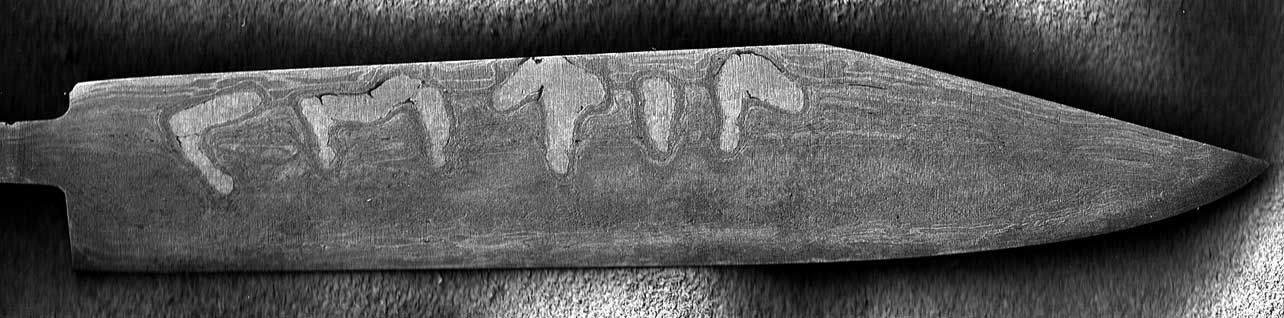
On this side the surface was not sanded down quite so far, you can still see some of the remaining cracks along the tops of the first two letters. This has resulted in a thicker deposit of the mild steel remaining in place. On this side is also visible a wide band that is a result of the random composition of the wrought iron.
On the whole, I am fairly pleased with the results - at least as a test of concept. A couple of modifications suggest themselves:
- Hot punch the pattern lines as a first step. The weld beads would then be set below the billet surface. Instead of pounding in (creating cracks) the excess weld material would simply be ground flush (quickly with an angle grinder)
- Substitute stainless wire for the mild steel in the MIG welder. This would produce significantly more contrast at the final etch. It also would allow the technique to be applied to mild steel as the base material.
Obviously this is NOT a substitute for the historical inlay method. It does however suggest design possibilities of its own. Adding patterns on to plate, then forging the flat plate into bowls as one idea...
That's a great idea for non-period "inlay."
ReplyDeleteBoth Jake and Jeff frequent Don Fogg's bladesmith forums, for those who want to see more work from either or both of these fine gentlemen.
I think the key to this would be hot punching first.
ReplyDeleteI was using one of those small 110 MIG welders for this. On consideration this might be the ideal tool. There is less penetration, but also the bead line itself is finer than what you might get with a heavier machine. Even still, there is a real limit to how fine a lie you can lay down with this method. So I think the application may be limited on blades.
As a decorative technique on larger forged sculptural pieces I do think this method holds some promise. I have a single (unfortuneatley) piece of wrought iron sheet from a turn of the century water tank. This stuff is about 1/4 thick and might prove ideal for the bowl project I mentioned.
I did notice another effect that might be worth exploring. After I laid the bead down, I compressed the raised lines to a flat surface by forging. On the line and dot side, most of the additional mild steel was ground away. The pattern was visible primarily as a distortion in the underlaying grain in the wrought iron bar. What if you did this with a layered steel billet as the parent bar? This might produce interesting patterns in the 'damascus' - with actually less material loss than more conventional cutting or punching then flattening / grinding.
Good GOD Man! This is the most interesting thing I have read in weeks! I learned the modern technique when I was in school for arcwelding but this is so much cooler!
ReplyDeleteThank you for sharing!!!!
Elrik the Bastard