(yet another Rant - skip this post if you are following the main topics of Iron / the Viking Age / Blacksmithing.)
"Its new, Its Better... Its Bullshit"
I spent yet another frustrating day accomplishing nothing wrestling with computers. I have not been able to complete a auction posting on E-bay for over two weeks. I get to the second last step in that tedious process of creating a new listing, only to get a 'Page not responding' error message.
Should you say - So WHAT, consider that I have several thousands of dollars in sales of my educational DVD's on E-bay to date this year. Like it or not, it has been a big component of my gross income, and why I got to eat in January and February.
I have had a number of back a forth messages from what passes for the Help Desk at E-bay. I suppose the staff there must be pretty to look at, it becomes apparent that they were not hired for brains. They fill the 'Walmart' definition of service: I'm happ-happ-happy and so help-help-helpfull - but I'm sot stu-stu-stupid. I get asked to include tedious details and retain every line back and forth in each message. Which no one on their end is even reading. This apparent because the same useless 'advice' is repeated from each new person that answers the question. The most standard 'solution' is for me to purchase yet another new computer and all new software, and to switch to a high speed line.
I spent well over FIVE HOURS yesterday attempting to spot the real problem. I tested my access into the internet (and specifically e-bay) via SIX different software browsers, on FOUR different computers, on TWO different phone lines, over FOUR different dial up points, and eventually TWO entirely different ISP companies.
The restriction is with the phone line. The copper cable that runs from my house via Bell Canada to the closest switching station, which is 20 kilometers away. The data transfer through this cable is running at roughly 2 kb per second. For those who don't know, I am a RURAL resident. This length of copper is my only option.
Two factors are a play here:
First is the general tendency of the whole world to speed up. Speed up whether there is actually any value to the increase or not. E-bay for example, keeps 'improving' the layout and function of their web site. It keeps adding lots of new features. Each of these takes more data time to transfer. I certainly find their web site does not FUNCTION any better. I really DO NOT WANT 'buddy lists' or any of that such crap. By making a site more complex (although not actually any 'better') they are in fact cutting access to those who do not have the 'latest and best'.
Second factor is the growing strain, and frankly collapse, of non urban support structures. The tendency over the last decade has been to devote resources to those structures that are utilized by URBAN residents. This could coldly be seen as applying 'bang for the buck'. Why provide new water pipes to that small community out on the fringes when for less money the service could be applied to a new suburban housing complex? Why upgrade phone or electric lines to MODERN standards for a rural area when so few people live there?
I understand the logic - at least on the surface. But unfortunately there is another factor at play - the increasing population density in rural areas. I live some 2 plus hours NW of Toronto, moving here about 20 years ago. I freely chose to live down a dirt road that gets pot holed, next to cows and subject to frequent blizzards. (I'm NOT one of those people who thinks a farming area is some kind of suburbia!) I expected power outages, being snowed under for days and even not being able to buy books around here.
But what has happened is that although there has been no upgrades to the support systems, the POPULATION has at least doubled in that same 20 years. Also of course that each individual home is placing an ever increasing demand on the existing grid. This is most extreme with the electrical supply, with now daily brown outs and 'flickers' at least once a week that temporarily shut down the power (just long enough to crash a computer and make us re-set a dozen internal clocks). Now it appears that the phone service is showing the same strain.
Now, I have spoken to 'worker bees' from both Bell Canada and Ontario Hydro. I have been told that there is absolutely no intention of upgrading the existing grid for either utility. All the resources are being concentrated to the major urban centres. Balance that against how in my region, there are twice as many homes all consuming much more power trying to pull out of the same old power grid. 'Go freeze in the dark'
Consistently, there has been a DECLINE in the available level of support available at my rural location since I made it my home. Out of three available hospitals inside a 30 minute drive, one has been closed entirely, one only offers Emergency Room 9 to 5 weekdays, and the third, while still open 24 hours, now only has a doctor 'on call' outside of business hours. We are supposed to be 'serviced' out of the regional trama centres - one of Barrie / Orangeville / Owen Sound. Any of those is 75 km or 45 minutes fast drive from home. If I have that stroke that runs in all my family at about my age - well, just kiss my ass goodbye.
Like all good Rants - this goes kind of no place. I don't have a solution. A plea for anyone in a position to make changes NOT to make changes that are based on mere speed for speed's sake. Ever more quickly, anyone not living in the large cities is being left in the dust.
Quite literally.
Darrell Markewitz is a professional blacksmith who specializes in the Viking Age. He designed the living History program for L'Anse aux Meadows NHSC (Parks Canada) and worked on a number of major international exhibits. A recent passion is experimental iron smelting. 'Hammered Out Bits' focuses primarily on IRON and the VIKING AGE
Sunday, July 30, 2006
Friday, July 28, 2006
"Reforging Iron in Pictish Scotland 850-1050AD
A version of a recent request and my reply...
Evelyn wrote:
"... I'm researching a novel that's set in the Aberdeen to Inverness area of Scotland around 850-1050AD with Vikings, Picts and Monks as characters.
... The author has asked me to find out what the process would be for a Viking youth in Scotland (who has been exposed to iron smithing techniques in Norway) to turn an iron candle sconce into a blade during this period."
Ok - the first main point is that you are looking at the skills of the blacksmith. There should be some information available on-line in a general sense here. DARC will have some images from our presentations at Heffenreffer in Rhode Island of a reconstructed Viking Age sand table style forge. The smithing equipment seen is largely based on the Mastermyr tool box. That collection is from Gotland, and although dated to 1150 contains all VA type tools. Check also the information on the Norse Encampment - under Artifacts
Second point relates to the candle sconce. Not really a Viking Age type of object. Its also likely to be a very bad choice in terms of its starting shape related to the desired finished knife shape.
The details I require are:
> What kind of tree was used to make the charcoal? (I've read the wareham forge page which says that types of wood didn't matter)
Exactly. Archaeology shows that charcoal used compares exactly with what ever trees were growing locally. I doubt peat would work. (Although I have heard rumors of attempts to use this.) Coal was not used until into the 12- 1300's. Hardwood works better than softwood. The thermal energy is similar pound per pound, but the hardwood requires less volume and keeps its shape longer. Oak would be one of your better choices if available. (At L'Anse aux Meadows they used the local black spruce and birch.)
What was the tree chopped down with?
Seriously? An axe...
How was the wood obtained from the tree?
Most likely just cut the whole thing down and render it into pieces. I think you may be hinting at the possibility of gathering wind fall branches. This is less work than cutting down whole trees, but really only is effective in a mature forest. Later in the Middle Ages they would coppice - grow a small plot of fast growing saplings set very close together. This gives a quick turn over of similar sized trunks, and is ideal for commercial production.
In any case, the manufacture of charcoal is its own lengthy process. The wood should be cut down or split to roughly identical diameter pieces. In the Viking Age, the most common method was to dig a shallow, wide bowl and then construct a bee hive shaped pile of wood splits - say 2 - 3 meters across and about 2 meters tall. Over the wood goes a layer of grass sods and earth. A hole is left in the top and a couple of holes at the base. Set the stack on fire. Once the burn is established, start blocking the holes with stones. Trick is to allow enough air (oxygen) into the inside to maintain a slow smoldering fire. Too much air and your just burn the wood to ash. Too little and there is not enough heat maintained to bake the wood to charcoal. This process can take days to accomplish. Once the pile stops off gassing heavy smoke the charcoal conversion has taken place. You would block all the holes, let the interior cool and then open it up.
The resulting charcoal would then have to be broken up to use in the forge. My own limited experience here suggests pieces from walnut to fist sized for the forge.
How did they store and dry the wood?
Ah - for making charcoal you want to use the wood 'green' - fresh cut. Saves that whole problem.
> Did they use a crucible to heat the iron object?
> What was the crucible (or similar) made of?
> What did it look like?
No - you are thinking of CAST iron, which was not used in any form at all until well past the Medieval period. The VA blacksmith would be forging his metals - heating and hammering them.
What else was required in the process?
VA forges are distinctive in that they use a block of stone, usually soapstone, to bank the fire up against. This specially made bellows stone has a hole in it that has the bellows attached on the other side.
Forges are often shallow bowls on the ground.
VA bellows are a distinctive double bag style. See the image on the web site for reconstructions.
Anvils in the VA are quite small. Typical is a rough cube about 10 cm to a side and maybe 5 - 10 kg. It is also possible to use a large flat rock.
There is some discussion about how an anvil would be mounted. This relates back to the body position that the smith would work in. Could be kneeling, hunkering or standing. A timber block to set the anvil on would be cut to the required height.
A good reconstruction of a VA blacksmith's shop can be found inside my exhibit 'World of the Norse'.
Could one person carry out the procedure?
Well - if you have to. Ideally there should be a second person (often a child or apprentice) pumping the bellows. The arrangement of the equipment makes it difficult to work the bellows then rush over to grab the metal to hammer it in the short time it is a working temperature. Charcoal also burns away quite quickly so the metal needs to be constantly re-positioned in the fire. The effective heated area in a VA forge is about 10 cm diameter at best.
What did they do to make it into something?
If starting from a normal 'currency bar' of wrought iron (a piece roughly 2 x 2 cm by about 20 - 30 cm long)
- draw source bar out into starting profile (for a knife something like 3 cm wide by maybe .5 cm thick by however long.
- forge the object
- see blade smithing below
> What tools were used to work the iron?
- hammer (roughly 800 - 1000 gms by the way)
- tongs
How blacksmiths worked?
No idea what you mean here. Obviously this is an open ended question that covers several books worth of description - or a lot of years at the forge. I'd suggest you track down one of the Medieval or Viking Age re-enactors in your area and ask if there are any working smiths in the group. I do know there are several in Australia. Watch them work. Also consider purchasing my own DVD 'Forging the Viking Age', which details production of a number of VA objects (admittedly using Victorian equipment).
The key is that forging takes a block of material and stretches it. No mass or volume is added, but some will be lost depending on how extensive the forging is. - see the bit below about clay
What problems would a novice encounter reforging iron?
Technically, any wrought iron object can be re-forged into a different shape. The problem lies in how easy it is to convert one shape into another. The more complex the shapes involved the more difficult this will be.
- A fast way to gain insight is get some clay and make a soft clay version of object one. Then try to squish that shape over into object two.
Any time you attempt to fold the clay - it's a forge weld. This is challenging to accomplish with a VA charcoal fire - and not work for beginners in any case. The odds are good a beginner would overheat and destroy the metal - or underheat and not get the weld to stick (more likely actually with this VA forge set up) Also expect to loose maybe 10% of your metal mass at each full weld step.
How difficult is it to make a blade?
Bladesmithing has its own problems. The metal you start with should be of different quality - higher carbon content - than what is used for everyday domestic pieces.
- see above. Effective bladesmithing also requires careful control of the hammer to produce an even stress on to the shape as it is forged out.
- After the shape is forged, it must then be polished. In the Viking Age, this would be done mainly by grinding the surface with hand held stones. This will take MUCH longer than the forging process. (Days instead of hours).
- Next comes the three steps of the heat treating. Anneal to soften and releave stresses. Harden by quenching. Temper to soften the blade slightly to give it the required flexibility in use. This was a 'mystery' and would not be discussed outside of the smith / apprentice relationship.
- Finish with applying the handle.
What would be involved in progressing from a blade to a sword?
In theory you could take several small knives and reduce them to flat bars. Weld the flat bars together to a larger block. Take that block and forge it out into the sword shape. Undertake all the polish, heat treat and hilting steps.
Now double all the difficulty due to the size of the object. Four times the difficulty for the heat treating. For the Viking Age equipment (forge and anvil size) increase difficulty by at least four times.
It might make more sense to consider taking several smaller objects of smaller size and various types and forge welding these into a layered steel billet. Again refer to the wareham forge site (bladesmithing) for a fast description of pattern welding. In its simplest form (often seen in the VA) use the harder metal from a knife as the centre with two outside slabs made from wrought iron from a meat skewer. Remember that a REAL sword weighs something about 1 kg. You'd need about a kilo and a half of metal to start (loss in welding and polishing).
Remember that the 'average metal load' per person in the Viking Age is in the range of 2 kilograms. (Modern North Americans have closer to 1000 kg or more!)
Generally swords are expensive objects - and highly specialized ones. They were often family heirlooms, and certainly not every male owned one. Multi function tools like axes or spears were far more common. The smiths who created them were also specialists. Pattern welded swords were the product of master smiths alone. Although your young hero may have been able to pound a straight section of metal from a cooking tool handle into a simple knife - if he had access to that axe to make the charcoal he would be more likely to just re-sharpen the axe and use it on his adventure.
Evelyn wrote:
"... I'm researching a novel that's set in the Aberdeen to Inverness area of Scotland around 850-1050AD with Vikings, Picts and Monks as characters.
... The author has asked me to find out what the process would be for a Viking youth in Scotland (who has been exposed to iron smithing techniques in Norway) to turn an iron candle sconce into a blade during this period."
Ok - the first main point is that you are looking at the skills of the blacksmith. There should be some information available on-line in a general sense here. DARC will have some images from our presentations at Heffenreffer in Rhode Island of a reconstructed Viking Age sand table style forge. The smithing equipment seen is largely based on the Mastermyr tool box. That collection is from Gotland, and although dated to 1150 contains all VA type tools. Check also the information on the Norse Encampment - under Artifacts
Second point relates to the candle sconce. Not really a Viking Age type of object. Its also likely to be a very bad choice in terms of its starting shape related to the desired finished knife shape.
The details I require are:
> What kind of tree was used to make the charcoal? (I've read the wareham forge page which says that types of wood didn't matter)
Exactly. Archaeology shows that charcoal used compares exactly with what ever trees were growing locally. I doubt peat would work. (Although I have heard rumors of attempts to use this.) Coal was not used until into the 12- 1300's. Hardwood works better than softwood. The thermal energy is similar pound per pound, but the hardwood requires less volume and keeps its shape longer. Oak would be one of your better choices if available. (At L'Anse aux Meadows they used the local black spruce and birch.)
What was the tree chopped down with?
Seriously? An axe...
How was the wood obtained from the tree?
Most likely just cut the whole thing down and render it into pieces. I think you may be hinting at the possibility of gathering wind fall branches. This is less work than cutting down whole trees, but really only is effective in a mature forest. Later in the Middle Ages they would coppice - grow a small plot of fast growing saplings set very close together. This gives a quick turn over of similar sized trunks, and is ideal for commercial production.
In any case, the manufacture of charcoal is its own lengthy process. The wood should be cut down or split to roughly identical diameter pieces. In the Viking Age, the most common method was to dig a shallow, wide bowl and then construct a bee hive shaped pile of wood splits - say 2 - 3 meters across and about 2 meters tall. Over the wood goes a layer of grass sods and earth. A hole is left in the top and a couple of holes at the base. Set the stack on fire. Once the burn is established, start blocking the holes with stones. Trick is to allow enough air (oxygen) into the inside to maintain a slow smoldering fire. Too much air and your just burn the wood to ash. Too little and there is not enough heat maintained to bake the wood to charcoal. This process can take days to accomplish. Once the pile stops off gassing heavy smoke the charcoal conversion has taken place. You would block all the holes, let the interior cool and then open it up.
The resulting charcoal would then have to be broken up to use in the forge. My own limited experience here suggests pieces from walnut to fist sized for the forge.
How did they store and dry the wood?
Ah - for making charcoal you want to use the wood 'green' - fresh cut. Saves that whole problem.
> Did they use a crucible to heat the iron object?
> What was the crucible (or similar) made of?
> What did it look like?
No - you are thinking of CAST iron, which was not used in any form at all until well past the Medieval period. The VA blacksmith would be forging his metals - heating and hammering them.
What else was required in the process?
VA forges are distinctive in that they use a block of stone, usually soapstone, to bank the fire up against. This specially made bellows stone has a hole in it that has the bellows attached on the other side.
Forges are often shallow bowls on the ground.
VA bellows are a distinctive double bag style. See the image on the web site for reconstructions.
Anvils in the VA are quite small. Typical is a rough cube about 10 cm to a side and maybe 5 - 10 kg. It is also possible to use a large flat rock.
There is some discussion about how an anvil would be mounted. This relates back to the body position that the smith would work in. Could be kneeling, hunkering or standing. A timber block to set the anvil on would be cut to the required height.
A good reconstruction of a VA blacksmith's shop can be found inside my exhibit 'World of the Norse'.
Could one person carry out the procedure?
Well - if you have to. Ideally there should be a second person (often a child or apprentice) pumping the bellows. The arrangement of the equipment makes it difficult to work the bellows then rush over to grab the metal to hammer it in the short time it is a working temperature. Charcoal also burns away quite quickly so the metal needs to be constantly re-positioned in the fire. The effective heated area in a VA forge is about 10 cm diameter at best.
What did they do to make it into something?
If starting from a normal 'currency bar' of wrought iron (a piece roughly 2 x 2 cm by about 20 - 30 cm long)
- draw source bar out into starting profile (for a knife something like 3 cm wide by maybe .5 cm thick by however long.
- forge the object
- see blade smithing below
> What tools were used to work the iron?
- hammer (roughly 800 - 1000 gms by the way)
- tongs
How blacksmiths worked?
No idea what you mean here. Obviously this is an open ended question that covers several books worth of description - or a lot of years at the forge. I'd suggest you track down one of the Medieval or Viking Age re-enactors in your area and ask if there are any working smiths in the group. I do know there are several in Australia. Watch them work. Also consider purchasing my own DVD 'Forging the Viking Age', which details production of a number of VA objects (admittedly using Victorian equipment).
The key is that forging takes a block of material and stretches it. No mass or volume is added, but some will be lost depending on how extensive the forging is. - see the bit below about clay
What problems would a novice encounter reforging iron?
Technically, any wrought iron object can be re-forged into a different shape. The problem lies in how easy it is to convert one shape into another. The more complex the shapes involved the more difficult this will be.
- A fast way to gain insight is get some clay and make a soft clay version of object one. Then try to squish that shape over into object two.
Any time you attempt to fold the clay - it's a forge weld. This is challenging to accomplish with a VA charcoal fire - and not work for beginners in any case. The odds are good a beginner would overheat and destroy the metal - or underheat and not get the weld to stick (more likely actually with this VA forge set up) Also expect to loose maybe 10% of your metal mass at each full weld step.
How difficult is it to make a blade?
Bladesmithing has its own problems. The metal you start with should be of different quality - higher carbon content - than what is used for everyday domestic pieces.
- see above. Effective bladesmithing also requires careful control of the hammer to produce an even stress on to the shape as it is forged out.
- After the shape is forged, it must then be polished. In the Viking Age, this would be done mainly by grinding the surface with hand held stones. This will take MUCH longer than the forging process. (Days instead of hours).
- Next comes the three steps of the heat treating. Anneal to soften and releave stresses. Harden by quenching. Temper to soften the blade slightly to give it the required flexibility in use. This was a 'mystery' and would not be discussed outside of the smith / apprentice relationship.
- Finish with applying the handle.
What would be involved in progressing from a blade to a sword?
In theory you could take several small knives and reduce them to flat bars. Weld the flat bars together to a larger block. Take that block and forge it out into the sword shape. Undertake all the polish, heat treat and hilting steps.
Now double all the difficulty due to the size of the object. Four times the difficulty for the heat treating. For the Viking Age equipment (forge and anvil size) increase difficulty by at least four times.
It might make more sense to consider taking several smaller objects of smaller size and various types and forge welding these into a layered steel billet. Again refer to the wareham forge site (bladesmithing) for a fast description of pattern welding. In its simplest form (often seen in the VA) use the harder metal from a knife as the centre with two outside slabs made from wrought iron from a meat skewer. Remember that a REAL sword weighs something about 1 kg. You'd need about a kilo and a half of metal to start (loss in welding and polishing).
Remember that the 'average metal load' per person in the Viking Age is in the range of 2 kilograms. (Modern North Americans have closer to 1000 kg or more!)
Generally swords are expensive objects - and highly specialized ones. They were often family heirlooms, and certainly not every male owned one. Multi function tools like axes or spears were far more common. The smiths who created them were also specialists. Pattern welded swords were the product of master smiths alone. Although your young hero may have been able to pound a straight section of metal from a cooking tool handle into a simple knife - if he had access to that axe to make the charcoal he would be more likely to just re-sharpen the axe and use it on his adventure.
Wednesday, July 26, 2006
Celtic Winds
What I've been up to # 3

This is part of the series of 'Windbiles' - wind motion pieces - I have been designing. In this case the lines are directly inspired from those found in Celtic Iron Age art. The Windbile series are a reflection of my work inside the Four Elements of the Ancients - Earth and Air, Fire and Water. The entire piece stands about 8 feet tall and is about 4 foot in diameter at the top and 18 inches at the base.
A spray of six 1/4" diameter round rods are joined to a rough carved granite base. These rods are slightly curved outwards, and range from roughly 5 to about 6 1/2 feet tall. They have been left as raw metal with a rust patina. Each is crowned with a vane made from curved aluminum sheet.
The starting piece for each vane was four feet long, and tapers from 6 inches at the top to about 3" at the base. The final roughly 16 inches has been cut back to create four separate fingers. The sheet has then been carefully curved in a distinctive series of terminal spirals and random interlocking reversal curves.
The thickness of the support rods is such that they will flex under the force of wind against the vane. The vanes themselves will also spring, slightly changing the orientation of the curves. The combination creates a continuous motion under even a gentle breeze. (It is suggested that the piece be mounted in a slightly sheltered location.)
Asking price for Celtic Winds is $400.
I will be also be making up some of the single rod and van combinations, on a slightly smaller scale. (Roughly 4 - 5 feet long with 2 x 4 x 24 inch long vanes). These will be intended to just be thrust into the ground as a garden decoration. Expect to find these at the Goderich Celtic Festival, August 11 - 13.
This is part of the series of 'Windbiles' - wind motion pieces - I have been designing. In this case the lines are directly inspired from those found in Celtic Iron Age art. The Windbile series are a reflection of my work inside the Four Elements of the Ancients - Earth and Air, Fire and Water. The entire piece stands about 8 feet tall and is about 4 foot in diameter at the top and 18 inches at the base.
A spray of six 1/4" diameter round rods are joined to a rough carved granite base. These rods are slightly curved outwards, and range from roughly 5 to about 6 1/2 feet tall. They have been left as raw metal with a rust patina. Each is crowned with a vane made from curved aluminum sheet.
The thickness of the support rods is such that they will flex under the force of wind against the vane. The vanes themselves will also spring, slightly changing the orientation of the curves. The combination creates a continuous motion under even a gentle breeze. (It is suggested that the piece be mounted in a slightly sheltered location.)
Asking price for Celtic Winds is $400.
I will be also be making up some of the single rod and van combinations, on a slightly smaller scale. (Roughly 4 - 5 feet long with 2 x 4 x 24 inch long vanes). These will be intended to just be thrust into the ground as a garden decoration. Expect to find these at the Goderich Celtic Festival, August 11 - 13.
Monday, July 24, 2006
Lebanon
Author's Note:
This a departure from my normal series. It is a pure POLITICAL OPINION piece.
Many are certain NOT to agree with these views.
Citizenship conveys Rights,
but more importantly,
Citizenship demands Responsibilities.
Its been another tragic week in the long tragic history of what is called the Holy Land. In my own times, there have been so many incidents, outrages and outright wars surrounding Israel that they blur together. How can anyone possibly claim that the latest events come as any kind of surprise? Since Israel was created, the whole region has been constantly at a boil. About every 10 years the lid explosively blows off. People in these ancient lands have been killing each other over religion for longer than humans have even had writing to record the history.
How can anyone claim that they could not have expected exactly the type of situation that is currently unfolding in Israel and Lebanon to take place at some point? If not this week, then next week, next month? And the whole bloody mess to repeat itself next year, or the year after that...
When you throw rocks at uniforms with guns - you should absolutely expect to be shot at. When someone fires a rocket across the valley from an apartment block - you should expect the response to be a shell from a tank. If you live in an area that is daily embroiled in the worst kind of violence, that of terrorism, you should not be surprised when you personally catch a piece of it. Any rational adult who has paid even the briefest attention to world events in the last 50 years knows this. If you want to avoid the heat - stay away from the fire.
Those who have left Canada to go into any unstable region - who have chosen to put themselves inside this pressure cooker - must bear some direct responsibility for their own situation. People have deliberately decided to travel, as 'vacation', to a known area of violence. There is a second group, those who have once fled the region, then once safely removed, have then returned to take up residence once again - of their own personal choice. If you desire safety, stay away from the combat zone.
Suddenly now, there is a demand for Canada to extract these same people from the region. To guaranty not only their safely, but unbelievably , of their physical comfort during the process. Endlessly we hear statements demanding servicing of these people's Rights. Yet any mention of Individual Responsibility is never heard.Adults are supposed to be responsible for themselves. People had some justification and obviously the money that allowed them to transport themselves into the region. They were either uneducated, foolish, or naive to think themselves immune to the violence around them. They were just plain stupid not to have an escape route and supplies at hand.
My simple question is this : Why do any of you think as a Canadian Citizen, * I * am now responsible for providing a fast and comfortable rescue to those who chose of their own free will to put themselves at risk in the first place? Those trapped during ill considered travel may have some call on Canada for aid. Those who claim Citizenship, but have now taken residency on troubled ground, do not. To add insult, there have been those individuals who at the same time have demanded the People of Canada provide and pay for their personal safety have also complained about how uncomfortable and inconvenient the rescue was. The alternative was to stay in your 'homeland' and take your chances with the Militants and the Army...
It is ironic that voices that decry any form of funding for the Canadian Military suddenly are the same ones demanding to know why those same ill-equipped forces are unable to respond instantly. Without paying the Piper, you will not hear a tune.
I have heard people who state their association with one or other of the various groups embroiled in the conflict call the others Racist or Anti-Semitic, Terrorist or Police State. By even expressing my own opinion on this issue, I am sure to be be condemmed - considered to be Anti-Immigrant and hopelessly Right Wing. So be it. I've taken my turn wearing the uniform of Canada. I have never been a 'hyphenated' Canadian.
A Citizen is one who Stands, who understands the Responsibility, not the just the Rights.
This a departure from my normal series. It is a pure POLITICAL OPINION piece.
Many are certain NOT to agree with these views.
Citizenship conveys Rights,
but more importantly,
Citizenship demands Responsibilities.
Its been another tragic week in the long tragic history of what is called the Holy Land. In my own times, there have been so many incidents, outrages and outright wars surrounding Israel that they blur together. How can anyone possibly claim that the latest events come as any kind of surprise? Since Israel was created, the whole region has been constantly at a boil. About every 10 years the lid explosively blows off. People in these ancient lands have been killing each other over religion for longer than humans have even had writing to record the history.
How can anyone claim that they could not have expected exactly the type of situation that is currently unfolding in Israel and Lebanon to take place at some point? If not this week, then next week, next month? And the whole bloody mess to repeat itself next year, or the year after that...
When you throw rocks at uniforms with guns - you should absolutely expect to be shot at. When someone fires a rocket across the valley from an apartment block - you should expect the response to be a shell from a tank. If you live in an area that is daily embroiled in the worst kind of violence, that of terrorism, you should not be surprised when you personally catch a piece of it. Any rational adult who has paid even the briefest attention to world events in the last 50 years knows this. If you want to avoid the heat - stay away from the fire.
Those who have left Canada to go into any unstable region - who have chosen to put themselves inside this pressure cooker - must bear some direct responsibility for their own situation. People have deliberately decided to travel, as 'vacation', to a known area of violence. There is a second group, those who have once fled the region, then once safely removed, have then returned to take up residence once again - of their own personal choice. If you desire safety, stay away from the combat zone.
Suddenly now, there is a demand for Canada to extract these same people from the region. To guaranty not only their safely, but unbelievably , of their physical comfort during the process. Endlessly we hear statements demanding servicing of these people's Rights. Yet any mention of Individual Responsibility is never heard.Adults are supposed to be responsible for themselves. People had some justification and obviously the money that allowed them to transport themselves into the region. They were either uneducated, foolish, or naive to think themselves immune to the violence around them. They were just plain stupid not to have an escape route and supplies at hand.
My simple question is this : Why do any of you think as a Canadian Citizen, * I * am now responsible for providing a fast and comfortable rescue to those who chose of their own free will to put themselves at risk in the first place? Those trapped during ill considered travel may have some call on Canada for aid. Those who claim Citizenship, but have now taken residency on troubled ground, do not. To add insult, there have been those individuals who at the same time have demanded the People of Canada provide and pay for their personal safety have also complained about how uncomfortable and inconvenient the rescue was. The alternative was to stay in your 'homeland' and take your chances with the Militants and the Army...
It is ironic that voices that decry any form of funding for the Canadian Military suddenly are the same ones demanding to know why those same ill-equipped forces are unable to respond instantly. Without paying the Piper, you will not hear a tune.
I have heard people who state their association with one or other of the various groups embroiled in the conflict call the others Racist or Anti-Semitic, Terrorist or Police State. By even expressing my own opinion on this issue, I am sure to be be condemmed - considered to be Anti-Immigrant and hopelessly Right Wing. So be it. I've taken my turn wearing the uniform of Canada. I have never been a 'hyphenated' Canadian.
A Citizen is one who Stands, who understands the Responsibility, not the just the Rights.
Pattern Welded Sgian Dubh
What I've been doing # 2
This is a custom knife created for a customer who wanted to mark his upcoming wedding with a distinctive heirloom object.

The knife has a 5 1/2 inch long pattern welded blade in a semi drop point style. The hilt is bog oak - in this case oak recovered from an original Roman era timber dock at the city of London, about 2000 years old. (What the English supplier told me was the source.) It bears Celtic knotwork carving on the right (out from leg) side and the owners name and wedding date on the inner.

The blade is formed of a total of four core rods - each at about 40 layers.
I started with a stack of 9 plates, then welded and folded in four. The starting stack was composed of mild steel / L6 alloy / wrought iron / high carbon tool steel. The sequence was M/I/M/L/H/L/M/I/M. This block was drawn and half was twisted. This section with the right and left twist was then cut and forms the two core rods along the back of the blade. The remaing half of the block was drawn out and cut in two. These pieces were then welded to another piece of carbon steel. When I count the lers (I include all four bars) the total layer count is 158. The decorative material is ground back to expose that hard carbon steel cutting edge.
This was a fairly complex project. The creation of the pattern welded billet was the most straight forward part, but is always quite time consuming. The bog oak proved quite difficult to get. This material is quite hard, working almost like copper metal. The surface carving was done with burrs on a rotary shaft.
This is a custom knife created for a customer who wanted to mark his upcoming wedding with a distinctive heirloom object.
The knife has a 5 1/2 inch long pattern welded blade in a semi drop point style. The hilt is bog oak - in this case oak recovered from an original Roman era timber dock at the city of London, about 2000 years old. (What the English supplier told me was the source.) It bears Celtic knotwork carving on the right (out from leg) side and the owners name and wedding date on the inner.
The blade is formed of a total of four core rods - each at about 40 layers.
I started with a stack of 9 plates, then welded and folded in four. The starting stack was composed of mild steel / L6 alloy / wrought iron / high carbon tool steel. The sequence was M/I/M/L/H/L/M/I/M. This block was drawn and half was twisted. This section with the right and left twist was then cut and forms the two core rods along the back of the blade. The remaing half of the block was drawn out and cut in two. These pieces were then welded to another piece of carbon steel. When I count the lers (I include all four bars) the total layer count is 158. The decorative material is ground back to expose that hard carbon steel cutting edge.
This was a fairly complex project. The creation of the pattern welded billet was the most straight forward part, but is always quite time consuming. The bog oak proved quite difficult to get. This material is quite hard, working almost like copper metal. The surface carving was done with burrs on a rotary shaft.
Sunday, July 23, 2006
Norse / Saxon fighting axe
What I've been doing # 1
This is actually a bit older, being one of several axes I created last winter. I had been contacted by Disney Imagineering to produce a number of reproduction objects for a presentation at Epcot in Florida. They were launching the new Norway display by having an exhibit of Viking Age artifacts on loan. They were then using the artifacts as the prototypes for the standing display.
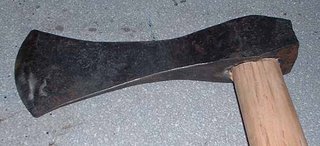
This axe ended up slightly different from the artifact sample I was working from. The slightly upsweep to the top edge is more typical of late Anglo Saxon axes. The overall length is 21 cm, the width at the edge is 9 cm, and the weight about 600 gms. The thickness at the eye is 4 cm. The head is forged from a single block of mild steel, which was then water hardened. This is also a punched eye - which is the correct method for Saxon and Viking Age axes. (Medieval to Settlement era axes in contrast are folded and welded). This gives a distinctive profile to the head, not normally seen in modern 'replicas' (often made from folded sheet and arc welded).
The head has been fitted to a contoured ash handle, 26 cm long. The weight and handle make it suitable for single hand use - but there is enough length to permit two hands as well. The blade is sharpened with a combat grind (way too thin for wood!).
This is a highly accurate replica, bracketing the time from 600 - 800 AD.
The asking price for this axe, complete, is $300 CDN.
Drop me an e-mail at : info@warehamforge.ca if you are interested.
This is actually a bit older, being one of several axes I created last winter. I had been contacted by Disney Imagineering to produce a number of reproduction objects for a presentation at Epcot in Florida. They were launching the new Norway display by having an exhibit of Viking Age artifacts on loan. They were then using the artifacts as the prototypes for the standing display.
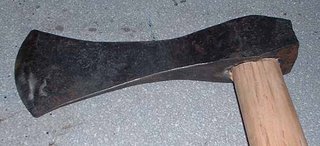
This axe ended up slightly different from the artifact sample I was working from. The slightly upsweep to the top edge is more typical of late Anglo Saxon axes. The overall length is 21 cm, the width at the edge is 9 cm, and the weight about 600 gms. The thickness at the eye is 4 cm. The head is forged from a single block of mild steel, which was then water hardened. This is also a punched eye - which is the correct method for Saxon and Viking Age axes. (Medieval to Settlement era axes in contrast are folded and welded). This gives a distinctive profile to the head, not normally seen in modern 'replicas' (often made from folded sheet and arc welded).
The head has been fitted to a contoured ash handle, 26 cm long. The weight and handle make it suitable for single hand use - but there is enough length to permit two hands as well. The blade is sharpened with a combat grind (way too thin for wood!).
This is a highly accurate replica, bracketing the time from 600 - 800 AD.
The asking price for this axe, complete, is $300 CDN.
Drop me an e-mail at : info@warehamforge.ca if you are interested.
Tuesday, July 18, 2006
Replica of the Gilling West Sword
A long standing commission has been a Viking Age pattern welded sword for my friend Neil Peterson. The original commission was many years ago, when I attempted a 2/3 scale replica based on Sutton Hoo. To make a long story short, I failed part of the final welding and the blade shattered on quenching. A heartbreaking loss of over 6 weeks solid work.
Although it has become a standing joke, I am finally starting slow work on a replacement sword. Neil's ideas and needs have changed over the years, so now the historic prototype is the Gilling West sword. This was discovered in 1976 at Gilling West in north Yorkshire. The preliminary report by Gilmour and Watkin classes the blade as a late Anglo Saxon / early Viking Age type. The approximate date (based on other similar swords) is from the late 800's. The overall length of the sword is 85 cm, the blade is 70 cm long and 5 cm wide at the hilt.
Gilling West is constructed of a bundle of SIX core rods, laid up 3 on 3, with a mono block edge. As with other complex core constructions, the individual core rods are alternating twisted and straight sections, plus alternating left, right twists down each rod. The actual layer count of the core rods is not estimated in the report.
For the replica's core rods, I am using a blend of wrought iron / mild steel / L6 alloy, with 9 layers in the starting billet. The iron is from a bridge built in Ohio in the 1860's. I have a good amount of this material and it is excellent quality. The plates are forged down from 3/4'" square to roughly 1" x 1/4" thick, so the thickness varies slightly. Many feet of iron had to be prepared. The mild steel is commercial 1 x 3/16' flat stock. The L6 is taken from bandsaw blades, the material here is 1 x 1/32" thick. L6 is a medium carbon (about .5%) carbon with a small amount of nickel (about .5%). In this case this material simulates the use of nickel-iron meteor iron. The end result of this mix should give a fiberous texture from the iron, a medium grey from the mild steel and bright silver lines from the L6, when etched. The overall average carbon content of the mixture should work out close to that of a mild steel - about .2 %.
Starting plates: left to right - wrought iron / L6 / mild steel
Bellow are the longer handle lengths of mild steel.
A total of 8 billets are being prepared, two more than are required.
The individual plates are about 6" long - a bit longer than the length I would normally use
(for knives about 4" to start).
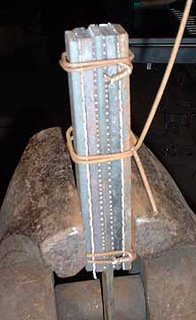
Showing one of the billet stacks being wired together.
Note the longer handle piece at the centre.
The order of plates is: M/L/I/L/M/L/I/L/M
I prefer to hold the plates together using fencing wire, three loops in this case.
The plan is to complete the sword by welding on two edge strips of a middle carbon spring steel. This is roughly the same mix as used on 'The Sword of Heroes' seen on the Wareham Forge web site. That earlier blade has only two core rods.
I will report on this project as it proceeds.
Although it has become a standing joke, I am finally starting slow work on a replacement sword. Neil's ideas and needs have changed over the years, so now the historic prototype is the Gilling West sword. This was discovered in 1976 at Gilling West in north Yorkshire. The preliminary report by Gilmour and Watkin classes the blade as a late Anglo Saxon / early Viking Age type. The approximate date (based on other similar swords) is from the late 800's. The overall length of the sword is 85 cm, the blade is 70 cm long and 5 cm wide at the hilt.
Gilling West is constructed of a bundle of SIX core rods, laid up 3 on 3, with a mono block edge. As with other complex core constructions, the individual core rods are alternating twisted and straight sections, plus alternating left, right twists down each rod. The actual layer count of the core rods is not estimated in the report.
For the replica's core rods, I am using a blend of wrought iron / mild steel / L6 alloy, with 9 layers in the starting billet. The iron is from a bridge built in Ohio in the 1860's. I have a good amount of this material and it is excellent quality. The plates are forged down from 3/4'" square to roughly 1" x 1/4" thick, so the thickness varies slightly. Many feet of iron had to be prepared. The mild steel is commercial 1 x 3/16' flat stock. The L6 is taken from bandsaw blades, the material here is 1 x 1/32" thick. L6 is a medium carbon (about .5%) carbon with a small amount of nickel (about .5%). In this case this material simulates the use of nickel-iron meteor iron. The end result of this mix should give a fiberous texture from the iron, a medium grey from the mild steel and bright silver lines from the L6, when etched. The overall average carbon content of the mixture should work out close to that of a mild steel - about .2 %.
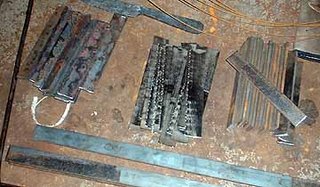
Bellow are the longer handle lengths of mild steel.
A total of 8 billets are being prepared, two more than are required.
The individual plates are about 6" long - a bit longer than the length I would normally use
(for knives about 4" to start).
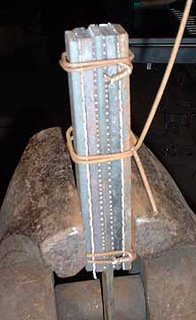
Showing one of the billet stacks being wired together.
Note the longer handle piece at the centre.
The order of plates is: M/L/I/L/M/L/I/L/M
I prefer to hold the plates together using fencing wire, three loops in this case.
The plan is to complete the sword by welding on two edge strips of a middle carbon spring steel. This is roughly the same mix as used on 'The Sword of Heroes' seen on the Wareham Forge web site. That earlier blade has only two core rods.
I will report on this project as it proceeds.
Tuesday, July 11, 2006
Defining the Smith (part 3)
Part 3 of the article 'Defining the Artist Blacksmith'
These are only the rough edits of the article as it was written. The full finishe text is being posted up to the Ontario Artist Blacksmith Association web site and available HERE.
On Production Methods:
There are obviously other methods of taking the modern raw material - lengths of industrially produced mild steel bar, and converting these into objects, be it practical or decorative in nature.
At one end of the scale will be the Welder. It is possible to purchase industrially manufactured elements, both structural and decorative, and assemble these pre-made pieces into a larger construction. More stress has been placed recently on the technical skill of welding through recent changes to the Ontario Building Codes. Obviously this type of work requires no direct manipulation of the metal in any form whatever. With care and a good eye, pre-made elements can be combined into effective designs, however this work is simply not Blacksmithing in any form.
On a level of complexity, the next step would be that of the Fabricator. In this process, some new elements are created by working metal stocks while cold over standardized jigs or using bending machines. These elements may be combined with the same industrial elements mentioned above. The results may be decorative elements that are distinctive to a workshop, but most commonly are repeats of standard patterns between individual objects. Once again, the forge is not used in the creation of forms, so this also is not Blacksmithing.
The most complex work will be that of the Blacksmith. Metal will be shaped hot from the forge. In the very best artistic work, each individual bar will be radically transformed from its original industrial shape. The true Artisan Blacksmith may work within a recognizeable style, but each object may be a one of a kind creation.
Be it a modern gas or more traditional coal fired, the forge remains the required heart of the true Blacksmith's method. Although technical ability is important to produce objects of quality, without a creative spark the work will not inspire the viewer.
Truth in Terminology :
We all know how retail stores and mere fabricators deliberately and knowingly misuse the technical language of the blacksmith to increase the value of their products in the eyes of the customer. Its also painful to admit that within the blacksmithing community itself there are those who have converted what were once technical terms into mere advertising copy. Unfortunately, this relatively recent trend has also been increasing in frequency. "Its just easier to tell them what they want to hear" is an explanation that is often given.
If those who have a genuine interest in the traditional skills of the Blacksmith are not informing and educating the general public on the true nature of this trade - who then will do this? All of us involved in the work of the Artisan Blacksmith have a double sided responsibility to both correctly use and continually define our specialized terminology to the public.
The first and quite selfish reason is that a clear understanding of the distinctive way that we work can only increase the perceived value of that work in the eyes of the public. Only a fool would continue to attribute Walmart prices to the skilled labour required to create a one of a kind forged metalwork.
The second, and perhaps most important reason to 'Say what you Mean, and Mean what you Say' is to uphold the tradition passed down to us from the ancient line of Blacksmiths that stretches behind us all. As part of a generation who had to re-discover so much from what had been an almost shattered tradition, may of us understand how easily that thread can be severed. As one line of Blacksmiths hands the hammer to a new generation of enthusiastic Artisans, it is crucial that the responsibility for preserving that hard won wisdom is passed on as well.
These are only the rough edits of the article as it was written. The full finishe text is being posted up to the Ontario Artist Blacksmith Association web site and available HERE.
On Production Methods:
There are obviously other methods of taking the modern raw material - lengths of industrially produced mild steel bar, and converting these into objects, be it practical or decorative in nature.
At one end of the scale will be the Welder. It is possible to purchase industrially manufactured elements, both structural and decorative, and assemble these pre-made pieces into a larger construction. More stress has been placed recently on the technical skill of welding through recent changes to the Ontario Building Codes. Obviously this type of work requires no direct manipulation of the metal in any form whatever. With care and a good eye, pre-made elements can be combined into effective designs, however this work is simply not Blacksmithing in any form.
On a level of complexity, the next step would be that of the Fabricator. In this process, some new elements are created by working metal stocks while cold over standardized jigs or using bending machines. These elements may be combined with the same industrial elements mentioned above. The results may be decorative elements that are distinctive to a workshop, but most commonly are repeats of standard patterns between individual objects. Once again, the forge is not used in the creation of forms, so this also is not Blacksmithing.
The most complex work will be that of the Blacksmith. Metal will be shaped hot from the forge. In the very best artistic work, each individual bar will be radically transformed from its original industrial shape. The true Artisan Blacksmith may work within a recognizeable style, but each object may be a one of a kind creation.
Be it a modern gas or more traditional coal fired, the forge remains the required heart of the true Blacksmith's method. Although technical ability is important to produce objects of quality, without a creative spark the work will not inspire the viewer.
Truth in Terminology :
We all know how retail stores and mere fabricators deliberately and knowingly misuse the technical language of the blacksmith to increase the value of their products in the eyes of the customer. Its also painful to admit that within the blacksmithing community itself there are those who have converted what were once technical terms into mere advertising copy. Unfortunately, this relatively recent trend has also been increasing in frequency. "Its just easier to tell them what they want to hear" is an explanation that is often given.
If those who have a genuine interest in the traditional skills of the Blacksmith are not informing and educating the general public on the true nature of this trade - who then will do this? All of us involved in the work of the Artisan Blacksmith have a double sided responsibility to both correctly use and continually define our specialized terminology to the public.
The first and quite selfish reason is that a clear understanding of the distinctive way that we work can only increase the perceived value of that work in the eyes of the public. Only a fool would continue to attribute Walmart prices to the skilled labour required to create a one of a kind forged metalwork.
The second, and perhaps most important reason to 'Say what you Mean, and Mean what you Say' is to uphold the tradition passed down to us from the ancient line of Blacksmiths that stretches behind us all. As part of a generation who had to re-discover so much from what had been an almost shattered tradition, may of us understand how easily that thread can be severed. As one line of Blacksmiths hands the hammer to a new generation of enthusiastic Artisans, it is crucial that the responsibility for preserving that hard won wisdom is passed on as well.
Wednesday, July 05, 2006
On Wrought Iron
(2nd excerpt from 'Defining the Artisan Blacksmith' - under construction)
Wrought Iron:
Is a specific type of iron metal. It is created using a special equipment that results both a distinctive physical structure and also a specific chemistry. All three of these factors combine to a metal that is quite different than modern steel alloys. 'Wrought' in this case refers to the hammering process required to compress and purify the spongy iron bloom that is extracted from a bloomery furnace. There will always be some microscopic layers of silica slag remaining within any wrought iron bar. It is this slag that gives this metal its distinctive fracturing pattern, breaking as short tendrils. "Iron' is the primary element in the metal, and unlike modern alloys, most wrought iron will have few other components. Typically wrought iron has extremely low carbon content, on a grinder the sparks will test as dull red balls. Wrought iron is an ideal material for the process of hand forging. It will remain workable over a wider range of temperatures than modern steels. It will tend to de-laminate as it is worked, requiring it to be re-welded to consolidate the surface (a step not required with steel). Any forge welding is considerably easier with wrought iron, where the slag incorporated within the material tends to float to the surface at welding temperatures, so that often no additional flux needs to be applied.
The modern steel alloys start replacing wrought iron when the Bessemer furnace was introduced about 1855. This new technology not only allowed for greater control in the iron smelting process, it also increased the volume of production by an order of magnitude. Both of these factors made the new steel more dependable in quality and also considerably cheaper than the old wrought iron. By the early 1900's very little of the older metal was still being produced.
The last commercial production of true wrought iron was stopped in 1974. There has been no new wrought iron produced * anywhere in the West since that date.
Any real wrought iron available for sale today will be reclaimed from structures being dismantled. Most commonly the material will be from structural elements from things like bridges. In some cases, larger diameter bars may be reworked down before being sold. A modern industrial substitute is sold, under the trade names 'Electric Iron', 'Rivet Iron' or 'French Iron'. These materials are in fact low carbon content steels, with a carbon content in the range of .05%, but still with the crystal structure of modern steel.
Typically, only small amounts in random dimensions of true wrought iron, often originally created in the 1850's, can be found. Often this collected by blacksmiths as personal stockpiles of these historic materials. Historic wrought iron is treasured for its easy working when hand forged and its better aging characteristics than modern steels. It also becomes an interesting addition to the mix when creating layered steels for knife making.
The term 'Wrought Iron' has undergone a radical shift in its meaning at the hands of popular culture. The term moved from the technical language of the blacksmith into a descriptive term used by antique collectors in the early 1900's. When referring to objects hand forged by blacksmiths in the Settlement / Colonial period, they were correctly described as being made of wrought iron. Eventually however, the definition became less exact, coming be used for any object that was hand forged - regardless of the metal content. Over time (into the 1950's, as blacksmiths disappeared) the term 'wrought iron' has come to refer to 'any piece of metal with a shape that is painted black'. Now objects that are composed of modern mild steel, formed cold, shaped by machine (even plasma cut!), and then painted black - are referred to as 'wrought iron'. This is almost as far from the correct meaning of wrought iron as its possible to get.
( * There are two exceptions. There are a small number of museums preserving the history of technology and industry. Some of these will conduct smaller scale demonstration firings of their historic furnaces. The metal produced is typically kept inside the museum community for restoration work. The second exception are the small group of people using experimental archaeology methods to rediscover what are often ancient and lost smelting techniques. Yields from these test smelters are quite small, typically 5 - 10 kg per firing.)
Wrought Iron:
Is a specific type of iron metal. It is created using a special equipment that results both a distinctive physical structure and also a specific chemistry. All three of these factors combine to a metal that is quite different than modern steel alloys. 'Wrought' in this case refers to the hammering process required to compress and purify the spongy iron bloom that is extracted from a bloomery furnace. There will always be some microscopic layers of silica slag remaining within any wrought iron bar. It is this slag that gives this metal its distinctive fracturing pattern, breaking as short tendrils. "Iron' is the primary element in the metal, and unlike modern alloys, most wrought iron will have few other components. Typically wrought iron has extremely low carbon content, on a grinder the sparks will test as dull red balls. Wrought iron is an ideal material for the process of hand forging. It will remain workable over a wider range of temperatures than modern steels. It will tend to de-laminate as it is worked, requiring it to be re-welded to consolidate the surface (a step not required with steel). Any forge welding is considerably easier with wrought iron, where the slag incorporated within the material tends to float to the surface at welding temperatures, so that often no additional flux needs to be applied.
The modern steel alloys start replacing wrought iron when the Bessemer furnace was introduced about 1855. This new technology not only allowed for greater control in the iron smelting process, it also increased the volume of production by an order of magnitude. Both of these factors made the new steel more dependable in quality and also considerably cheaper than the old wrought iron. By the early 1900's very little of the older metal was still being produced.
The last commercial production of true wrought iron was stopped in 1974. There has been no new wrought iron produced * anywhere in the West since that date.
Any real wrought iron available for sale today will be reclaimed from structures being dismantled. Most commonly the material will be from structural elements from things like bridges. In some cases, larger diameter bars may be reworked down before being sold. A modern industrial substitute is sold, under the trade names 'Electric Iron', 'Rivet Iron' or 'French Iron'. These materials are in fact low carbon content steels, with a carbon content in the range of .05%, but still with the crystal structure of modern steel.
Typically, only small amounts in random dimensions of true wrought iron, often originally created in the 1850's, can be found. Often this collected by blacksmiths as personal stockpiles of these historic materials. Historic wrought iron is treasured for its easy working when hand forged and its better aging characteristics than modern steels. It also becomes an interesting addition to the mix when creating layered steels for knife making.
The term 'Wrought Iron' has undergone a radical shift in its meaning at the hands of popular culture. The term moved from the technical language of the blacksmith into a descriptive term used by antique collectors in the early 1900's. When referring to objects hand forged by blacksmiths in the Settlement / Colonial period, they were correctly described as being made of wrought iron. Eventually however, the definition became less exact, coming be used for any object that was hand forged - regardless of the metal content. Over time (into the 1950's, as blacksmiths disappeared) the term 'wrought iron' has come to refer to 'any piece of metal with a shape that is painted black'. Now objects that are composed of modern mild steel, formed cold, shaped by machine (even plasma cut!), and then painted black - are referred to as 'wrought iron'. This is almost as far from the correct meaning of wrought iron as its possible to get.
( * There are two exceptions. There are a small number of museums preserving the history of technology and industry. Some of these will conduct smaller scale demonstration firings of their historic furnaces. The metal produced is typically kept inside the museum community for restoration work. The second exception are the small group of people using experimental archaeology methods to rediscover what are often ancient and lost smelting techniques. Yields from these test smelters are quite small, typically 5 - 10 kg per firing.)