This is a fast overview of the conduct of the smelt undertaken on June 10 at Wareham. The iron masters were Kevin Jarbeau and Dave Cox, with primary assistant Ken Cook. Darrell Markewitz provided some technical advice (but an attempt was made to keep me out of it!). General background labour by other members of DARC.
The event was open by invitation to a select group of observers. Some members of the wider blacksmithing and the early period re-enacting community joined DARC for the day. We were also fortunate enough to have a couple of academic researchers present.
The smelter was of the general form of the 'Norse Short Shaft' type. This is a form of smelter that the group has past experience with. In this case the smelter has been constructed in a 'half banked' arrangement. The new smelting area features a short earth bank re-enforced with concrete blocks about 60 cm high. A hole was cut into the bank, roughly 45 cm in diameter and tapering slightly towards its base. The smelter was set into this bank, with its mid line at the line of the bank.
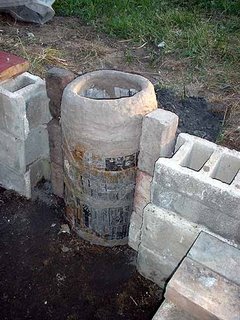
The smelter itself was constructed from clay cobb, a mix with dried wild grasses pulled off the yard. A powered commercial ball clay was used. As with past smelters, the cobb was compacted between two metal forms to speed construction. This all resulted in a cylinder about 25 cm internal diameter, 65 cm tall, with walls roughly 7.5 cm thick.
The smelter was constructed on May 30. The metal forms remained in place for about two days, and then were removed. (The paper seen serves as a separator to keep clay sticking to the metal.) At this point the gaps at the front edge of the smelter and block wall were filled with bricks. The space between the smelter and earth was filled with a mix of ash, sand, and burned charcoal and slag from an earlier smelt. This was then covered with a mesh feed bag to air dry.
In the two weeks till smelt day, the smelter settled under its weight down into the lightly compacted earth. This moved the floor of the smelter down about 5 cm. Some slumping at the base and thickening of the walls at the base as well - although both effects were minimal. Although the upper areas of the cobb were fairly hard and dry, the base areas were still quite damp and plastic.
The day before smelting, the tuyere was mounted and tap arch cut. The tuyere was set about 45 cm down from the top of the smelter, at the standard 22.5 degree down angle. The tip of extended in 5 cm beyond the smelter interior wall. The tap arch was located at the base as close to 90 degrees offset from the tuyere as was possible, roughly 20 cm wide by 13 cm tall.
At this point a wood splint fire was started, and allowed to burn for several hours. Eventually a heavy dished metal plate was put over the top opening to allow the coals to bake the structure overnight.
On the next day, the base of the smelter was determined and positioned with charcoal fines, roughly to the top of the tap arch (about 7 cm below the centre of the tuyere tip). preheat with wood was started about 9 am, switching to rough charcoal after 70 minutes (marking the official start time). Graded fuel started at plus 40 minutes. Air was supplied via the standard vacuum blower used in the past at about 700 litres per minute. The first ore charge was added at about plus 1 hour 15 minutes. The ore used was the Virginia rock ore (thanks to Sauder & Williams at about 65 iron oxide).
As with past smelts, constant time intervals were used to judge consumption and thus determine amounts of ore to add. A standard 2.2 kg / 5 lb bucket of charcoal was added at intervals ranging from 8 to 12 minutes, most at the 8 - 9 minute marks. The smelter proved very predictable in this rate. Ore was added using standard scoops (measured at 410 gm, but in practice closer to 370 gm).
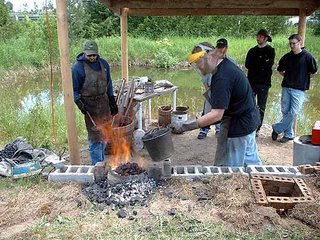
In the past a smelter would 'take off', increasing consumption after the addition of roughly 3 - 5 kg of ore. In this firing, this DID NOT happen. The consumption remained constant at one bucket plus one ore charge every 8 - 10 minutes for an extended period of time. At plus 6 hours, single ore charges were still being made. At this point it was decided to increase ore charges regardless of consumption rate, and starting at plus 6 hours 20 minutes. There were some gromps on hand from the October 2005 smelt, these were added in roughly 300 gm handfuls starting at about plus 7 hours.
At plus 7 hours 20 minutes the existing charges were allowed to settle to tuyere level. Two charcoal buckets and 10 minutes latter a shock charge of about 1 kg (three scoops) was added. Again this was allowed to settle, with the last charcoal added at plus 7 hours 50 minutes.
The burn down phase lowered the burning charcoal to about half the smelter height. Starting at about plus 7 hours 55 minutes, the air was reduced and the remaining charcoal was scooped out to the top of the tuyere. The mass was then compacted / loosened by use of the Thumper. Any large masses were separated from the smelter walls and extracted from the top using Bloom Tongs. The tap arch was then opened and material was raked from the bottom to clear the smelter interior.
Meanwhile, the group of blacksmiths under the leadership of Lloyd Johnson had constructed a simple ground pit forge to one side of the smelting area. This had a brick lining and a length of 2.5 cm ID pipe as the tuyere. Air was supplied by a hand cranked blower. Fuel was a combination of rough charcoal, bituminous coal and metallurgical coke. A hard wood stubb set to normal forging height (about 90 cm). As it turned out, this equipment was not going to be required.
When the smelter was opened, the hoped for bloom was not in evidence. The majority of the ore had been converted to cast iron. This material had solidified to a plate attached to the bottom of the slag mass, but also had formed a liquid pool below, burning down into the charcoal fines base. This liquid flowed out when the tap arch was opened. The slag mass itself was mainly attached to the smelter wall across from the tuyere. Below the tuyere were two smaller iron masses, each about fist sized. These are relatively porous forgeable iron blooms.
Total duration of smelt - 8 hours 10 minutes (not including preheat of 1 hour 30 minutes)
Total charcoal consumed - about 100 KG (plus preheat, forge)
Total ore added - about 18 KG
Yield - iron blooms - 1550 gm (as two fragments)
- cast iron - 1.3 KG (one larger piece plus small fragments)
- about 1.5 KG magnet fragments of partially sintered material gathered from smelter interior with a magnet.
- there was also considerable partially sintered ore remaining adhered to the smelter interior walls (unknown total)
There was some disappointment that our objective was not reached - to produce a historic sized bloom in the range of 5 - 8 kg. In retrospect, the long delay before adding larger sized charges to the smelter is most likely the reason for the production of so much cast iron material. With only a single charge added at a time, there would have been ample reaction of available carbon in the smelter column to create the carbon rich cast material.We think that this would have been the main product during the long drawn out middle action of the smelter. The smaller workable blooms are likely the result of the final decision to increase charge amounts latter in the smelt.
Regardless, the general operation of the smelter remains successful. Iron ore was certainly converted to metallic iron. Some more experience and confidence on the part of the iron masters would have led to an earlier modification of the amount of ore added. This in turn would certainly have increased the size of the bloom produced.
No compacting of the bloom fragments has been undertaken at this point. Expect a final report on what is discovered as the blooms are worked. Details of the experiment sequence and a photographic record will be available soon on the DARC web site.
No comments:
Post a Comment