REVIEW - What it is: IRON SMELTING
Smelting is the process of taking raw iron ore and converting via extremely high temperatures into a mass of workable metal. In the European 'Dark Ages' (post Roman through to the Crusades) the technology is roughly similar. A quick overview : The furnace used has heat resistant walls and is roughly the size of a 5 gallon pail on the inside (likely a bit taller). Inside this air is forced through a hole or pipe (the tuyere) to allow charcoal to burn. This not only produces the temperatures required (roughly 2400 F / 1100 C) but also produces the various gases required for the chemical changes. If everything goes EXACTLY right, after four to six hours the bottom of the furnace will have a bowl of glassy slag with a mass of metal (the bloom) resting inside of it. In Viking Age Scandinavia the ore type is almost always some variation on primary bog iron ore and smelters are located close to the source. Exact raw material preparation, charcoal used and smelter construction are then adjusted to relate all these locally available elements.
The bloom then needs to be extracted. It will have a lacy outside layer, which needs to be either hammered off or compressed into the bloom. Then the mass needs to be cut into pieces small enough to be worked by hand. Next the pieces are compressed to blocks, then worked into bars by repeated hammering, folding and welding. (Al this hammering is why the product is called 'wrought' iron )The end result is a 'currency bar' - typically about 2 cm square and about 30 - 40 cm long (say 3/4 x 12 - 18 inches). These bars are often seen flattened on one end and with a carry loop on the other. (This is how you blacksmith's purchase your metal buy the way - consider how this relates to producing that darn tripod.)
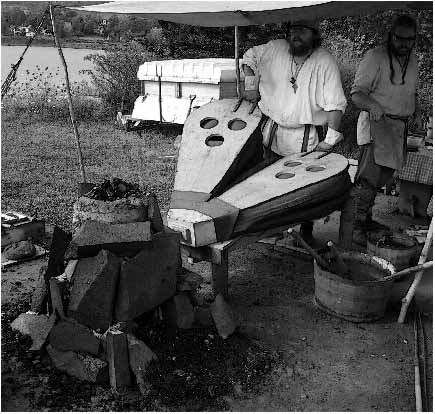
Problems:
The physical remains related to iron smelting from the Pre Conquest period are * extremely * limited:
- The furnaces themselves are relatively fragile, and so only the simplest remains are likely. With a clay furnace the upper sections (from just below the tuyere entry and up) will be baked to a simple ceramic. This is very porous, and water plus freeze and thaw quickly shatters it into a pile of small fragments. Only the very base of the cylindrical smelter is normally found. As this is not exposed to heat, what you find is a ring of mud.
So : what is the exact shape and layout of the furnace? It turns out that position of the tuyere and total height are quite important.
- Tuyere tubes or fragments are found. They almost all have a uniform interior diameter of 2.5 cm / 1 inch.
- The glassy bottom 'slag bowls' are found. Often located such that they are as they were formed at the base of a smelter. (Often the only indication of the size of the smelter or rough guide to the size of the bloom which was produced.) Problem here is that these are only the frozen remains formed at the very last stage of a complex series of chemical and physical reactions over a furnace use of several hours.
- Some finished blooms have been found. This does give us some idea of possible bloom sizes and quality. A range of roughly 5 - 8 kg seems to be common for the Viking Age.
So : why are these specific blooms recovered at all? Given the effort ("cost" in labour in materials) is there some specific reasons these blooms were retained or even discarded?
- No bellows remains from the Viking Age (at least after serious digging I have be unable to find a single artifact). There are two carved illustrations of * blacksmith * bellows. One is a side view with human figure for (possible) scale. The other a top view for proportions.

To mess this all up, modern experiments have demonstrated that the air volumes required for a successful smelt (producing an artifact type bloom) require something in the order of 5 times the volume of air possible from that blacksmith bellows.
So : are we looking for a different sized bellows? Are small bellows ganged together? Maybe an entirely different design? Maybe even an entirely different smelt sequence? All these have social implications as well, what evidence may there be of that aspect?
- There are no tools specific to the smelting process that have been found. (Again, I have not seen anything *** PLEASE !!!! *** if anyone knows of any, let me know!) We know from our own experiments that a number of specialized long handled probes, hooks, rakes - if not out and out necessary. Some of these need to be all metal to allow them to be driven by hammer blows. Add special oversize 'bloom tongs'. Heavy hammers are required, but at least other finds (like Mastermyr) show those. There are a number of wooden buckets and scoops that are either standard or would not leave any trace.

So : Are there any specialized 'smelt master' burials? Were ALL the large metal tools re-cycled? Is there some social reason why smelting tools were treated differently than blacksmithing tools? (Conversations with Dr. Kevin Smith suggest that this may be the case ?)
- There are no specific clothing items that have been found that relate to the very real protection problems quite specific to iron smelting
So : I'm going to put that into another post!
Darrell
A reference:
www.warehamforge.ca/ROMiron
No comments:
Post a Comment