Posted Today, 07:10 AM
The Evenstad hearth is a relatively shallow. With the 'high' tuyere level being 3 in. above the floor, it doesn't need to be more then 5-6 in. deep max.
...
The one depicted on Darrell's site is a smelting furnace. Much like a Catalan smelter. It is MUCH bigger then a hearth smelter....
So, sorry if this seems way to elementary, but I'm bearing in mind my own (lack of) experience in this specific area (re-melting hearths) - and the variation in background of the various readers.
The Aristotle Re-melting Furnace:

This is Lee Sauder at 'Smeltfest 2009' (This is the invitational research week Lee has hosted for a small group for a number of years.) That year Skip Williams introduced us to the 'Aristotle Furnace', which we worked with over about 30 plus test firings, building maybe a half dozen different layouts. (see a brief report : http://warehamforgeb...y-overview.html )
This is obviously a furnace - and a re-melting furnace (rather than an ore to metal 'smelter'). What it produces is a small puck of mid to high carbon metal, but with some of the slag inclusions and texture of a bloomery produced material. As Jan so correctly states, the source metal can be almost anything. We have tested this using pieces of mild steel bar, bits of cast iron window sash weights, old corroded wrought iron scrap, fragments of bloom - even nails and beer caps (!) The carbon content of the end product depends on the set up of the interior bottom of the furnace. You can both reduce *or* increase carbon content, depending on the bottom depth below the tuyere and the angle of blast.

Descriptions and further reading on the Web:
"Teeny-tiny Bloomery"
by Skip Williams
"A different way to make steel"
by Jesus Hernadez (on 'Don Fogg's Knife Forum')
Aristotle's Steel
by Lee Sauder (PDF download)
"Steelmaking in a tiny open furnace"
Donald Wagner (This is a photo essay from the same event that Lee's article above was based on.)
Because of the way this post works, I'm not sure how the order of the next images as attachments:
Re-Melting Hearth

The image is of Lee's experiments at Smeltfest 2012. The first I saw him working with that system was at Smeltfest 2011, working with Tim Young from the UK.
Note that I personally have never built or worked with one of these. This is also the core of the discussion here (!)
For that reason I am not going to attempt to describe how it works or what is going on - or the quality of the product. Mark certainly is covering that information (and well!).
Just for interest - although it is sideways to the main thread (and people have mentioned it)
Evenstad Bloomery Iron Furnace

This image is from Espelund's 'Iron in Norway', but is a reprint of the original 1782 manuscript illustrations by Evenstad.
One important note : The scale is in 'ells'. Think roughly the distance from your elbow to your finger tips with fingers extended. Given other places in the document as '60 cm'.
That makes the conical furnace roughly :
60 cm at the base
10 cm from base to tuyere
180 cm at the open top
120 cm deep
This is a wood fired furnace. The description states small pieces of wood would fill the furnace before lighting. The heat of combustion converts this to charcoal. Once this is accomplished, then the ore is added.
The furnace is intended to be a continuous cycle of production. Ore is added, reduced to a bloom. At that point the bloom is fished out from the top. The excess slag mass is cleaned, then the still hot furnace is filled with another charge of wood to repeat the process.
The bellows shown are two long narrow chambers, lifted with spring poles. A worker stands on top of the plank extensions, shifting his weight side to side to operate.
The source reference is:
Arne Eseplund : 'Iron Production in Norway During Two Millenia'
1995, ISBN 82-992430-3-3
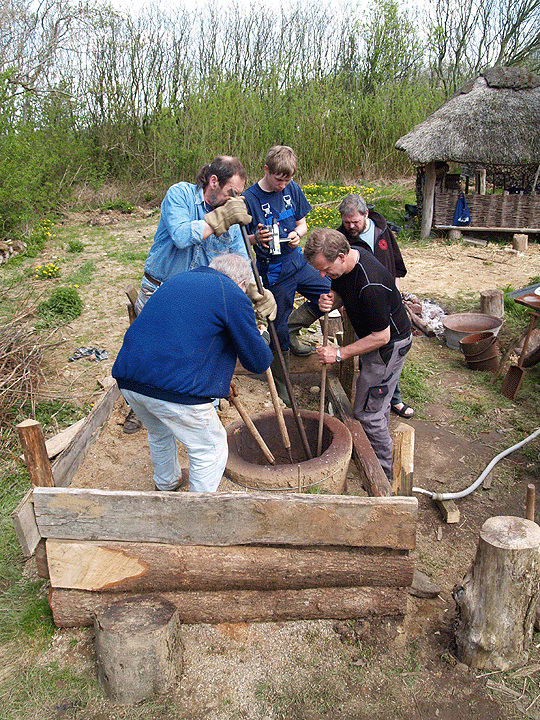
At the 2008 Heltborg Symposium, I saw Ole Nielsen and his team build a version of the Evenstad Furnace and operate it. Ole is to the left, blue shirt, gloves with long bar. (for more images see http://www.warehamfo...BORG/index.html ) This was still early in their experimental series, and although they did manage the wood to charcoal element, and produce a large slag mass, there was little iron produced. (Most of us had low or no yields, I think the ore we were using was to blame.)
This all started with Mark Green describing some of his recent experiments / tests using a deep hearth to refine and change the carbon content of his blooms. The conversation drifted a little, towards defining terminology:
Jan Ysselstein, on 07 January 2013 - 12:32 PM, said:
I have begun to associate a hearth as a furnace where the bottom plays a significant role.
As frequent readers know, the problem of use (and mis use!) of metal working terminology is a big concern for me.
No comments:
Post a Comment