I had started in an earlier post to talk about a current commission, for a heavy camp knife made in the pattern welded style. (
see : 'Some Layered Steel Billets')
After getting dragged into some pieces talking about the application of layered steel technique in the Viking Age, I wanted to detail the final production steps of the actual project underway.
(
see : 'Reinventing Layered Steels' / ' More on Pattern Welding' / 'Layered Steels - On Materials' )
Note: a number of the images here are fairly large, as they are direct scans shown at life size.
The customer had originally asked to have a knife based on this commercial one, the '
Kalinga' by well known manufacturer Buck Knives. He wanted the blade composed of pattern welded material, with olive wood slabs on the handle.
Now, those who have checked my
past work, or other commentaries here on Hammered Out Bits, know that I will not duplicate the designs of other artists. So I cautioned the customer that although I would use the Buck design as a starting point, both the forging process and my own ideas about blades and design would result in a finished knife that would be 'inspired' by, but not
duplicate, the reference.
After a false start (read 'screw up wasting three days work') I produced a large flat bar of pattern weld.
The starting stack of plates was : M/H/L/M/I/M/I/M/L/H/M . The finished construction was two twisted rods plus two flat layers with carbon core, with a total layer count of 265.
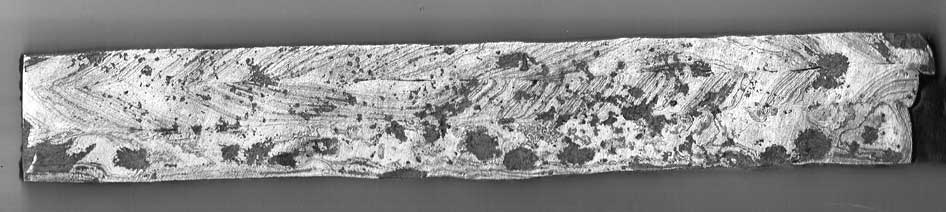
The process of forging up the starting billet took me three forge sessions (basically three work days). The next day I forged the blade out to rough shape. After drawing a basic point, I cut into the bottom edge (this time!) and lifted forward the material that would form the integral guard. Next the hilt end was forged to shape. Finally the actual bevel for the cutting and false edge where forged. The last step was to even up the overall profile, and ensure the blade was flat and square. The finished forging was then placed back inside the (gas) forge and allowed to sit overnight as the containment cooled, providing the annealing stage.
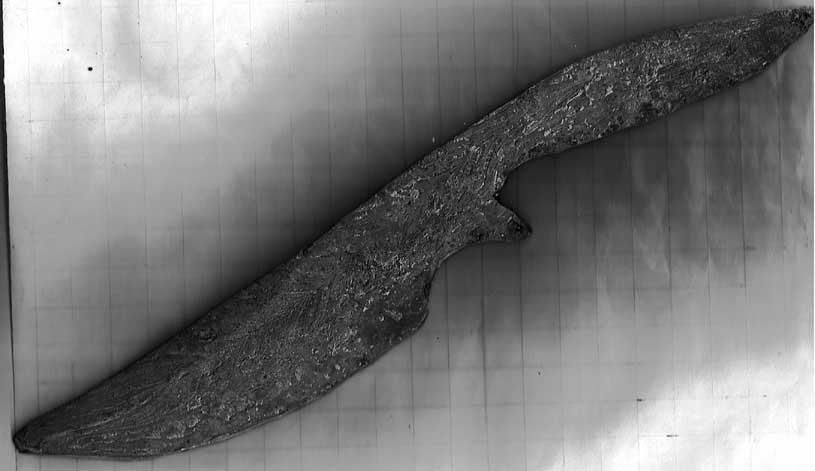
The next work is the fairly tedious process of grinding and polishing. First the rough forging was cleaned up with grinders. A bench grinder was used to even out the profiles. The blank was clamped and a hand angle grinder was used to first clean off the heavy scale from the annealing process. The work with angle grinder was then continued to both generally flatten the various surfaces, but also to cut down to remove any surface flaws. Holes for the final attachment of the wood slabs were made. Add another afternoon work session.
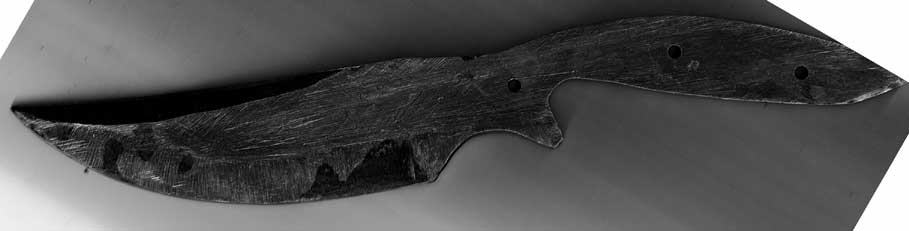
At this point any serious flaws from the welding process are visible. You always hope that there are either none, or that these are superficial cracks that will be removed by polishing.
From here, the next step is to completely flatten the various surfaces, polishing these smooth. I don't have a professional knife grinding machine (several thousand dollars). I do have a 6 x 48 inch belt sander 'hopped up' with a 2 x speed electric motor. Even still, the process of the first polishing step, at 60 or 80 grit, is by far the most tedious. At the same time you have to stay attentive. One slip of angle or position of the blade on the sander gouges the metal. Then the whole surface has to be reduced even further to remove that error. Add another full day work.

This first polish step is then followed by others. I personally do not find high polish surfaces functional. It also seems pointless to create a mirror polish, requiring many steps, then acid etch that surface off. So I made only one second polish, to 100 grit in this case. The image below shows the right side, with my makers mark clearly hot punched into the base of the blade.

Once polishing is complete, the next step is to harden the blade. The normal for me is to oil quench, as the core of the cutting edge is most typically a simple high carbon tool steel (in this case a 1095 file).
If there are any serious, but hidden, welding flaws, this is when they will appear. Often dramatically!
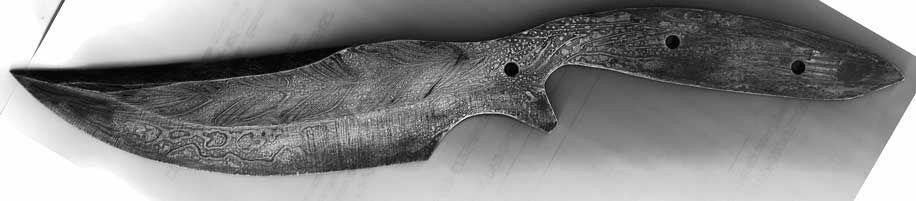
One other thing that becomes clear at this point is a first idea what the final patterning will look like. The differing alloys in the layering oxidize during the heating before quenching at differing rates. The mottled effect seen just back of the blade / hilt line is an effect of oil splashing up on the parts of the metal not submerged in the quench. This is just a surface effect.
The next step is to prepare the blade for tempering. As the temper colours are the effect of a subtle oxide film on the surface, you now have to polish the blade once again. I normally step up one grade, in this case polishing the blade itself to 120 grit. I find it easiest to control the application of heat on tempering with a hand propane torch.
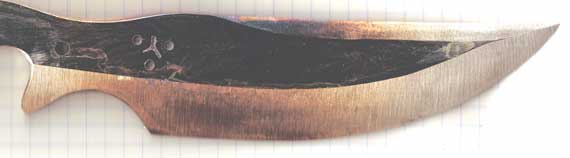
This is a direct scan of the final temper colours. The dark band along the flat of the blade is an effect of the scanning process, and the colours are not terribly accurate. The temper is only really significant for the lower half of the blade, as the carbon core is what is critical to effect here. (Remember the blend of hard and soft layers in the twisted bars along the back automatically create flexibility there.) The bulk of the cutting edge is pulled down to a dark straw, with just a hint of blue to purple at its top. The point has been left at quench hardness.
Now, if this was a plain single alloy knife, there would have to be yet another polishing step to remove the temper colours. Because the knife will now be etched, this extra step would serve no purpose.

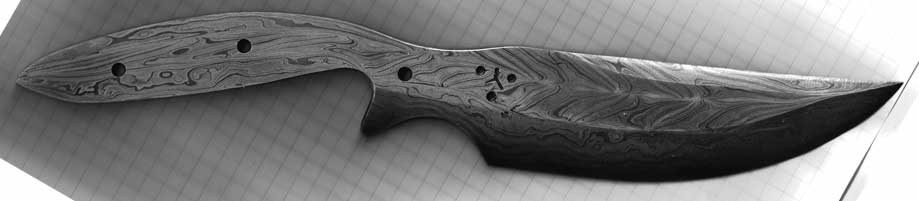
Now, those you you who have been following my recent work will realize that normally I like to make one piece knives, where the hilt is just an extension of the pattern welded material. Left to my own choice, I would have skipped the addition of wood slabs. (These of course will cover up the expensive patterned metal!) An extra day's worth of fairly complex steps have been added to reach this point.
For this commission however, the customer wanted to have wooden slabs attached.
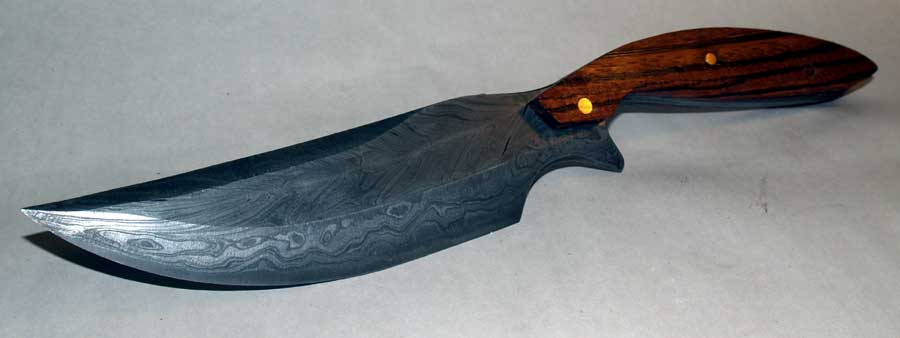
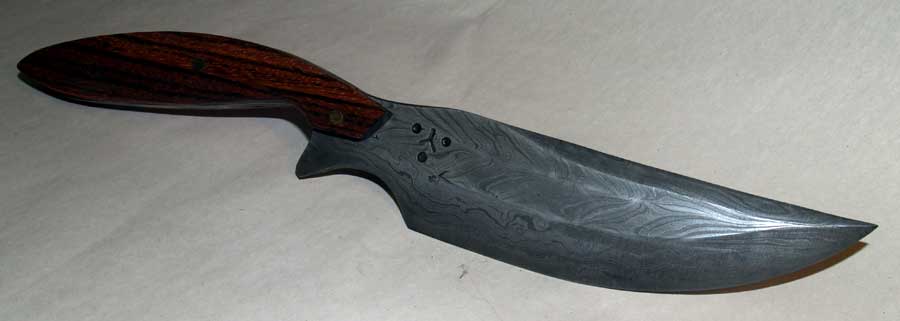
So this is the finished knife, the pattern on either side. Originally the wood slabs were to have been olive wood. It turned out that I did not have enough of that material, and the piece I did have had an extremely un-interesting grain pattern. I replaced the olive with more dramatic African Zebra wood, which had a similar colour range (tan with dark brown grain lines). The supporting pins are bronze. Add another three hours work.
One last thing:
The change in lines from the commerical source pattern allowed me to make a significant change in the handling of the completed knife. You see that the angle between hilt and blade is a bit different, the blade is heavier and longer. These combined to shift the balance points.
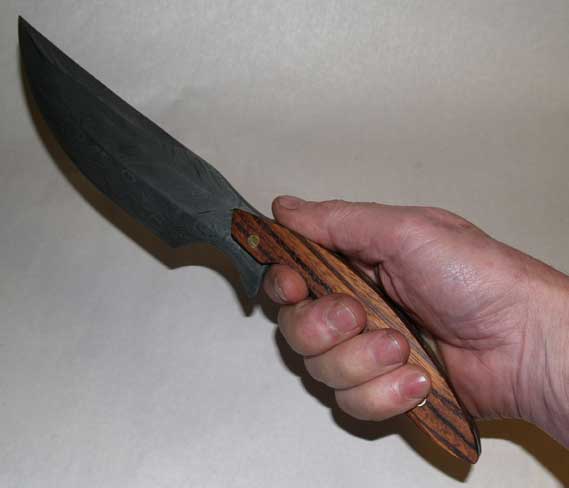
With the knife held in a more 'conventional' grip, fingers in the grooves behind the guard, the heavy blade sets the balance forward. This encourages a heavy, hacking motion, like you would use for cutting kindling. The blade is thicker than common, a full 1/4 inch, and also almost two inches wide. This produces an extremely strong blade that can produce a heavy stroke.
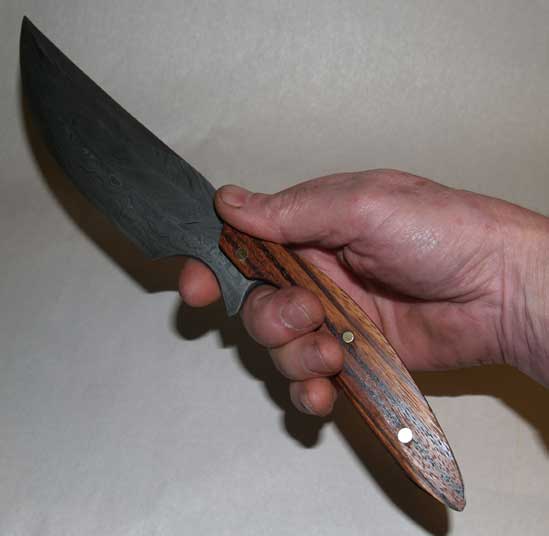
However, I deliberately not only changed the lines at the hilt, I also increased the size of the riccasso (just forward the guard). Gripped with thumb in the groove at the top, and fore finger in the riccasso, the balance shits dramatically. Now the weight sits back in the center of the hand, effectively lightening and 'speeding up' the motion at the tip. The blade ends in a sweeping curve, more typical of skinning knives. Despite the knife's large size (at 12 1/2 inches total), in this grip there is ample control of the front curve for skinning use.
I was extremely pleased with the overall results of the entire process - roughly seven 'shop days' from start to finish.