Mike's weird idea this time was 'stick it too it'. Instead of our standard slow ramping up of ore from a single scoop / pound per charcoal charge (4 lbs in this case), we STARTED ore charges at close equal amounts of ore to charcoal. This amount was increased from that level to about as large an amount as the smelter could stand. The maximum ore additions reached 6 lbs per bucket, with 4.5 lbs each 9 minutes being the averages.
Rather than try to insert another table on to the BLOG - I will just send you off to the Wareham Forge / Iron Smelting area. If you want to see the field data for this smlt - go HERE
(www.warehamforge.ca/ironsmelting/Early Iron 3/EarlyIron3-B.html)
The smelter was a re-use of the standard Flue Tyle teaching / experimental test bed developed by Lee Sauder & Skip Williams. They had set this up for a Saturday demonstration smelt, which was undertaken by Mike assisted by Lee. The furnace was in pretty good shape, just needing a bit of patching with clay around the tap arch and the tuyere. For the Monday smelt I used one of my normal ceramic tube tuyeres, but one of Lee's high volume blowers. (Sorry - I don't have air volume numbers for these - but it would be the range of 1000 litres per minute.)
The overall numbers were a bit surprising. Roughly 100 lbs of the Virginia Rock ore were charged (about 45 KG). Because of the high ore additions, considerably less charcoal than normal was consumed, roughly 130 lbs total (58 kg). The smelt was also faster considering its volumes - about 4 1/2 hours altogether (plus an hour for pre-heat).
The end result of this smelt was a very nice solid bloom. Extraction was basically from the bottom. Unfortunately there was no large sized scale on hand to get a finished weight. The bloom was slightly consolidated, then sectioned in half, and one half into quarters.
Lee and Mike had been working in the forge most of the day on a sculptural piece created from the bloom they had made on Saturday. Normally I'm pretty beat after a day long smelt, but they were keen to compress my quarter section to see what the quality was. Under Lee as forge master, with most of the striking labour supplied by Mike, and some contribution of myself as second striker, the section was forged to a very faithful replica of a Viking Age anvil.
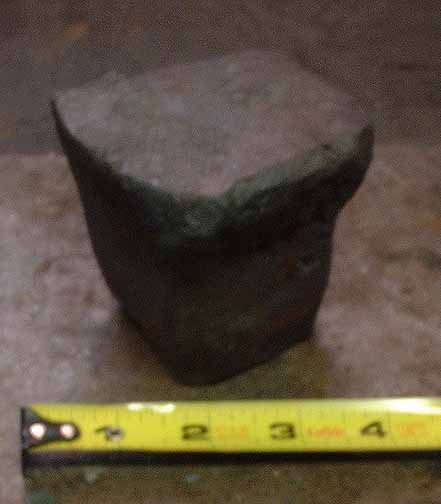
The finished object is rough cube 3 inches (7.5 cm) on a side. Finished weight is almost exactly 2 kg (roughly 4 1/2 lbs). It tapers slightly to the base (to permit solid mounting in a wooden stub latter). One of the sides shows fracturing, but it was decided to leave this crack as is rather than weld it shut. This was done to accent the nature and origin of the source material. At this point the surface is just hammer flattened. I have not decided if I will actually further smooth or polish the face. As it is the anvil will certainly serve its function. Right now the remaining three faces have two differing rough radius curves and one section that is relatively sharp. Again these edges could be dressed to even them up, but they will certainly prove functional. Lee's estimate of the relative carbon content (based on his extensive experience forging out blooms) is that this iron is some place between a 'pure' wrought iron and a modern mild steel in carbon (say equivalent to a 1010 material).
We all were extremely happy with the result. Although there are no measurements of the starting weight of the bloom before forging, the comparison of the ore weight to finished object is of note. Although not an exact ratio, the finished production yield is roughly 18% - considerably better than has been suggested by some other researchers
Darrell
No comments:
Post a Comment