This new bellows is being built for Neil Peterson, primarily for use in his experimental series related to Norse glass bead making.
The frame and layout is the same as that was used for the reconstruction of the Viking Age blacksmith's bellows. For details on the logic of the reconstruction, I refer you to earlier posts on that topic.
This bellows was constructed using only two of the lens shaped leathers. This gives a maximum possible loft of about 38 CM - which in practical use actually works out to the 36 cm total on the illustration. Any wider than that and you are stretching against the leather. Remember that our working numbers were something around 30 cm.
This image shows the internal contruction. I put a thin sheet of metal as a half circle on the inner side of each of the parts of the inlet valves. Note that there is a rim of leather left loose beyond the metal - this overlaps the size of the hole and remains flexible to make a better seal. The metal is roughly the same size as the hole in the plank.
You also see the inner support to the leathers. This is a piece of 1/2 x 1/8 flat which is bent to the same shape as the outline of the plates. This limits how much the bag can expand or collapse in under the pressures of filling or expelling. (Note that my set does not have this stiffener - instead it is double seamed with a piece of heavy wire inserted.
The second image shows the difference between totally collapsed and totally open.
First you see that totally collapsed, the effect is that the top plate sits parallel to the bottom one, at the same level as the top of the head block. This marks the 'dead air' at the maximum limit of an exhaust stroke. In actual practice, you might not actually stop as low as this.
So for calculations, only the upper triangle shape (illustration below) is available for air delivery.
One other thing to note is the way the sides of the leather bow in, even with the stiffener, at maximum fill height. This effect is actually more pronounced if the plate is not raised to maximum.
There is a slight opposite effect as the plate is lowered. You do notice that with the plate at the bottom of the stroke, the bag has collapsed in again. So I think the flexing of the leather bag is more significant in terms of limiting INTAKE, than in reducing output.
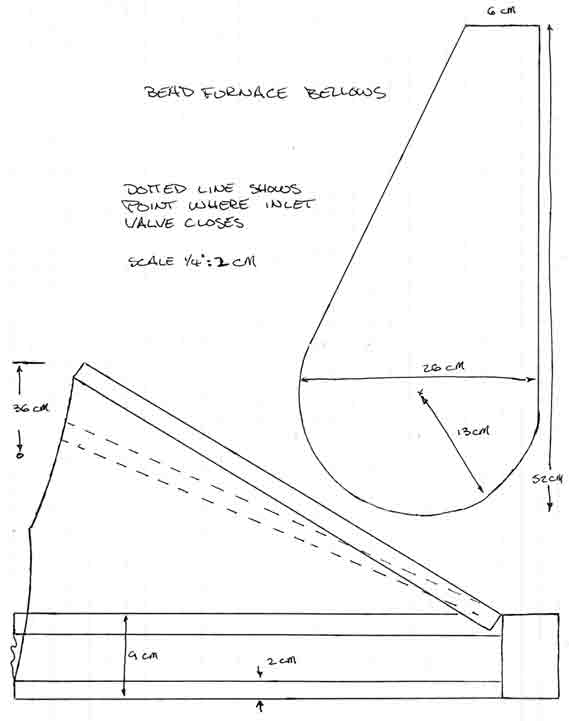
What is most sigificant to our calculatons is an effect we have not considered, which is 'valve lag'. This system requires some (significant) time for the valves to fully close at the start of an exhaust stroke. The valves are forced closed through two effects, a kind of inertia lag, plus the force of air outwards as the chamber is compressed. I think the wrist snap that Mark taught us works by mainly increasing the action of the inertia effect. In any case, there remains a significant difference between the top of the inlet stroke and the actual sealing of the valve (and thus the air available as exhaust volume). Its pretty darn hard to measure this working along (or maybe at all without much more sophisticated instruments). I estimated the difference was about 5 - 6 cm. I also suspect that this would be a relatively 'fixed' mechanical effect. At our standard 30 cm loft, the working seal would still be achieved at a drop of 5 - 6 cm. This means something about a 15% loss right off the top.
Jens Jørgen (at the Heltborg Museum in Denmark) is using a bellows with the valves located on the bottom plate. With that system, gravity is the first effect on closing the valves rather than inertia. I suspect this greatly reduces this potential loss - and would explain why he gets such good air volumes from his equipment.
I do think this reconstuction is more efficent than my set of the same size. The smaller bag (less folding) and stiffener both make for a larger fill volume. Tests will tell. I still don't think these are close to the required volumes for an iron smelt in practice however.
1 comment:
I also fought the valve lag problem, but came up with a different solution: Multiple valves. In the same way as a biturbo reduces the inertia of a combustion engines turbo, it reduces the Mass of each single valve and thus the time it needs to shut. With the valves to the bottom, the performance may be good, but you have a much higher chance of burning bellows because the valves opens later and requires considerable vacuum to open. If unexperienced people turn the bellow, it can lead to hot air ingestion and ignite the bellows exhaust valve block. You can counter burning of the bellow from inside with a longer and thinner air path, but this in turn reduces efficiency again and puts a higher strain on the bellows compresion capability. I'd like to keep my air path short and wide to avoid too much backpressure.
Post a Comment