polymarkos commented
"I ... chose charcoal simply because I can make it for little more than the labor."
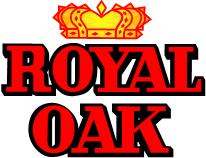
We consume a LOT of charcoal here when iron smelting, in the order of 50 - 100 kg per individual smelt event. DARC has been extremely fortunate that ROYAL OAK has donated several skid loads of charcoal to us over the years. We just would not be able to continue our experimental series without this kind support.
I have used charcoal from a number of commercial suppliers over the years. The very best was supplied by a local small scale operation : Bruce Cowen's Black Diamond Charcoal. Bruce was interested in charcoal production from wood lot debris the same way I am interested in iron smelting. He had designed a small retort a bit bigger than a water heater which, although simple in construction, was returning something like 90 % charcoal from wood by volume. His product was excellent quality, bone dry, and he even pre screened the material to the correct size for our uses! Unfortunately, Bruce ran afoul of the Ontario Ministry of the Environment, who shut his charcoal operation down. Too much smoke being generated. Blame a neighbour?
The worst was 'Cowboy' brand, I believe not available in Canada, which was used for Early Iron 2. This was made from used hardwood railway ties. It was inconsistent in both size and quality. Often there were large pieces not even converted from the source wood. We were pulling out rocks the size of a fist and rail spikes from the bags.
The weirdest was the material used for Early Iron 3 (I can't remember the brand name). This was a brand imported from Brazil, charcoal made from mix rain forest trees. The wood started as trees being cleared to expand pasture land. The bags made great note of the 'environmental' aspect of the source. (Frankly, better not to cut the rain forest down in the first place.) I found that this material was just inconsistent in terms of species, with both hardwood and softwood mixed. The tropical hardwoods did produce good temperatures, but seemed to create more ash than what is typical from the usual mixed oak and hickory used for North American charcoals.
The comment from 'polymarkos' relates back to making your own charcoal. Smelting gurus Sauder and Williams make their own, using a retort made from a converted garbage dumpster. Lee does live back in the hills, and will pretty much fill the hollow with smoke when the thing is running. Key to the economy (and consistancy) is that they can get free offcuts from a local hardwood trim mill. They have less labour on the preparation and no real cost (gas money) for the material.
We did look into making our own charcoal here at Wareham.
First thing, although I do live in the country, my home is only an acre lot, so I can't cut my own wood. I would have to purchase the wood, which I can get as quartered fire wood. The cost of this material (Fall 2009) is roughly $275 = $300 CDN per bush cord (delivered).
Now, assuming you did not loose too much in the conversion process, the pile does not change much in terms of actual volume - its the raw weight that changes. This as the water and other volatiles are driven out during the baking process. To effectively get uniform charcoal production all the pieces of wood need to be uniform sizes. This would mean axe splitting all that wood (delivered as quartered tree trunk sections) down. My best guess here would be to pieces roughly the size of your wrist. Starting with a pile 4 feet wide, four feet high and eight feet long, that process alone would certainly take me a day or two. (Frankly, I've never spit that much wood in one solid go.)
Admittedly, if you owned your own bush lot, the ideal material for making charcoal would be the branches from those trees you felled when cutting your winter fire would only. There would be a large reduction in labour, cutting to long lengths and mainly the effort of gathering the stuff. ( Utilizing this 'waste' wood was what got Bruce Cowan interested in the process). But as I said, I don't have access to a wood lot.
Now, I can't really comment personally on the charcoal making process. I do know that any charcoal kiln or pile requires constant monitoring and adjusting during the process. This to control the amount of air / oxygen available inside. To much, and the wood simply ignites and burns away. Too little and there is not enough heat available to keep the charcoal smoldering and driving off the volatile components. My friend (and another iron smelter) Mike McCarthy has done simple covered stack charcoal burns. He reports " We burned about 3/4 of a cord of wood, and produced some 17 bushels of good useable charcoal." in a process taking three full days. He gives this amount as enough to run two full iron smelts (so that would be about 200 kg of charcoal) Based on Mike's direct experience, that full bush cord would expect to create about 260 kg charcoal.
At retail the cost (locally, Ontario, from a bulk supplier) I pay $15 per 8 kg bag. So that same amount would be costing me about $500.
So compare - self made at $300 plus five days work : against purchased at $500 plus two hours drive.
5 comments:
After you get sick of being an overworked charcoal burner, you can go on to being a bodger. Except wood is evil.
Off topic but figured best way to reach you is to comment here. CAn you post to an answer to this question I ran across on an armour forum?
Hi everyone,
does anyone here have any hard data on slag content % in various armour finds from iron age up to 1066? Mainly I'm researching maille, but I'd also be interested in helmets and lamellar.
Cheers, RIchard Larmer
"Looking through arcehological reports from maille found at Vimosse, Birka, Gjermundbu and some other, the otherwise detailed scientific documentation notes riveted iron maille simply as containing "high slag content". I'm searching for more exact data on this, as in exactly what percentage constitutes high in these cases."
Andrew
Someone had mentioned this in a comment to an earlier post here:
ttp://books.google.com/books?id=GpVbnsqAzxIC&dq=The+Knight+and+the+Blast+Furnace:+A+History+of+the+Metallurgy+of+Armour+in+the+Middle+Ages+%26+the+Early+Modern+Period+(History+of+Warfare,+12)&printsec=frontcover&source=bn&hl=en&ei=FXToSvWjHY2uMIysrbMI&sa=X&oi=book_result&ct=result&resnum=5&ved=0CBEQ6AEwBA#v=onepage&q=The%20Knight%20and%20the%20Blast%20Furnace%3A%20A%20History%20of%20the%20Metallurgy%20of%20Armour%20in%20the%20Middle%20Ages%20%26%20the%20Early%20Modern%20Period%20(History%20of%20Warfare%2C%2012)&f=false
"The Knight and the Blast Furnace"
I have done no more than do a fast spot check, to see if it was worth going back and reading in detail (it looks like it)
I would also refer you to the Royal Armouries people at Leeds England (though I know their research wing got really axed last year).
If you really come up dry, I could try posting your question to the ArchMetals newsgroup??
Me - nothing else to point to.
Darrell
Andrew
this is an ugly way to communicate, please post me privately!
I asked Bill Short, who specializes in Viking Age weapons and Iceland in general:
Vegard Vike did an analysis of the Gjermundbu mail and several other contemporary specimens, which including analyzing slag inclusions. He didn't publish it, but I got a copy from him to which was used for the weapons book. I believe there a version on line which may or may not be authorized."
http://southtowerarmouringguild.blogspot.com/2009/08/assay-of-armour-in-malta.html
There you go Andrew....on a silver platter no less.
Post a Comment