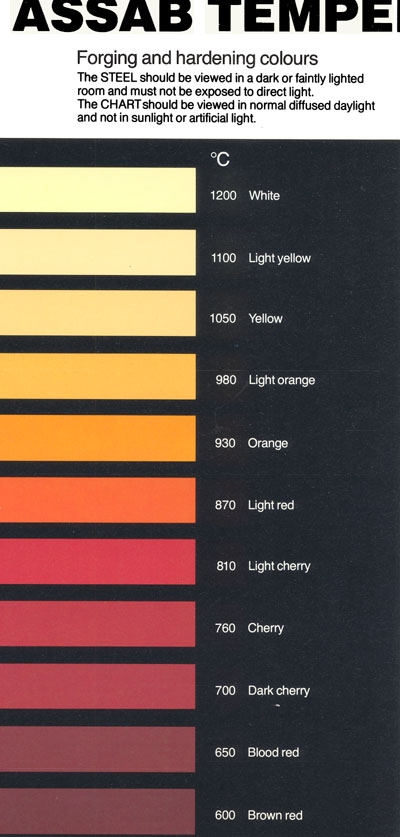
I would ask those reading this to refer to the industry standard 'heat colour to degree' chart I posted on my own iron smelting web pages.
You notice that it is in Celcius. This itself is a bit problematic, as working smiths typically only use colour references in the workshop. It also says that the chart is to be viewed in 'normal diffused daylight' (what ever the heck that is). This is critical, as the available light determines the observed colour significantly. If you were in sunlight, you would not even be able to perceive temperature colours below about 760 on the chart. I work inside, in a light controlled shop. If you have visited any working or historic shops, you always find them with few windows, so the lighting is constant and controlled (and thats why). Personally, I also wear dydymium safety glasses, which pretty much knock my observed colour back one grade off the chart. I primarily fire coal and propane, with some work with charcoal.
I don't cut the colours the way this chart does. If you consider paint colours (ie - you never had someone else say 'thats red') you would see that 980 is really a yellow, 870 is really an orange. Remember most the current generation of smiths (now the 'last generation', I've been at this a while) were largely self taught (in North America anyway). So our knowledge is based on direct experience - not what others have told us. This becomes significant in any discussion of 'best temperature to do what'.
Related to this - do NOT trust published photographs! Cameras, both digital or film, respond to infra-red light much differently than the human eye does. The typical published image will show the light from hot metal at least two grades higher than what your eye would perceive. (A good example here is the image used in this blog's title block!)
The series of red colours extends over a considerable range. Yes, you can shape a piece of metal in the red series of temperatures without damage. So by the chart I mean from 810 down as low as 600. But the amount of force needed to create the same effect at 810 is almost double that required at 930. The current wisdom is 'work smart - not hard'. People watching often wonder why I seem to create shapes so quickly. Yes, I have a lot of experience swinging the hammer. The biggest reason that I can work so fast is just working at higher (softer metal) temperatures. I normally *return* the metal to the fire at roughly 830 by that chart. (Thats a point most of beginner smiths are just *starting* to work.)
One topic that comes up constantly is 'what temperature / colour do you forge weld at'. Theoretically, if the steel surfaces are perfectly *clean* and perfectly *flat* you could weld at room temperature. If the two surfaces are in absolute intimate contact at an atomic level, the atoms will bond across the gaps. Now effectively you can't achieve this in the presence of oxygen. (Space craft have suffered 'vacuum welding' between polished surfaces.) If you are *very good* you can forge weld at lower temperatures. I have seen it done in demonstration, but frankly consider it an ego trip that misinforms novice smiths. So readers should take care when someone maintains they weld at lower temperature ranges, especially if you are seeking to learn this process. Its more a credit to the experience, rather than an example of the ideal method.
Fluxes for forge welding is a whole different topic!
Everyone keeps forgetting that the most effective working temperature also depends on the exact alloy you are working. Wrought iron is much softer than modern mild steel, even at room temperature. You can effectively move wrought iron at lower temperatures than the same mass of steel would be shaped. This is balanced however, by wrought iron's tendency to de-laminate, which means you have to bring it up for welding (to the top end of the range). My experience is that modern mild steels work most effectively in the orange ranges, so thats roughly 1000 through to maybe 850. As you select higher carbon contents, the materials become more rigid at the same temperatures. The typical method used to still get effective work undertaken is to work the metals at higher temperature ranges. The nickel / stainless and more exotic modern alloys become even more resistant to being deformed, even at the higher temperatures.
Next - heat sources:
My charcoal experience ranges from casting and forging using Viking Age equipment, and of course iron smelting.
In absolute terms, a kilogram of carbon will oxidize (burn) and create a fixed number of heat units. So a kilo of propane, charcoal or coal all creates the same temperature.
The problem in heating metal is getting that energy applied effectively to the metal involved.
First, remember that the Norse did in fact heat metal to welding temperatures - and beyond. The only fuel available to them is charcoal. So, yes, you can create all the temperature, applied to even larger objects (consider boat anchors) in a charcoal fire. An iron smelter runs at an effective 1200 C (or more) using charcoal. As has been pointed out, the design of the furnace and the volume of the air blast determine the effectiveness of heating. A hardwood camp fire is effectively hot enough to bring mild steel into the orange range, but the heat is too spread out to make it a truly effective heating method.
Someone had asked 'how fast'.
Using a small flask shaped furnace burning charcoal, you can completely melt the end of a 1 cm square bar, from cold, in about five minutes.
This is more or less a 'useless' bit of information. Just how fast a given piece of metal will heat to the effective working temperature for a given job depends on so many variables. It takes as long as it takes. (Its one of those questions anyone who regularly demonstrates in front of the public comes to hate.)
What everyone forgets is the effective COST of running various metalworking fires.
Propane is actually the most expensive of the fuels, both in terms of cost per kilogram and in terms of cost per work completed. Its advantage is that it is widely and easily available. Coal is typically the cheapest (this depending on if you can even get correct smithing coal in your region). Remember home heating coal (anthricite) is NOT the same as blacksmithing coal (bituminous).
I do purchase coal in 500 plus kg lots, and my propane as standard '40 pound' cylinders. My Chev Astro barely holds the volume of 300 kg of charcoal. (Thats a volume of just over 4 x 4 x 8 feet)
Those truly interested in this kind of comparison should look at an earlier comparison of fuel types against carbon release.
In my own home area in Ontario Canada - comparing current cost (January 2010) in CDN dollars per lb (sorry)
Propane - $0.88
Smithing Coal - $0.42
Hardwood Charcoal - $0.73
Again, these are somewhat useless numbers. My propane forge consumes roughly 2-3 times the mass of fuel per working hour as a coal fire does. Its a giant torch which remains full blast the entire time. A coal or charcoal fire is only rapidly consuming fuel when the air blast is applied, which is only when metal is to be heated. Charcoal is also requires a massive volume of fuel, as the material itself is so light. This effects the potential upper limit of the fire, as increasing air flow would just effectively blow the particles right out of the fire box.
Some argument might be made that charcoal is 'better' than propane. Its certainly not as effective in heating larger objects, or getting into the top temperature ranges. Why? Because the individual fuel particles are not very dense. You are consuming fuel so quickly, you have to constantly be adding new (cold) pieces to the fire. Try using charcoal to forge an axe, the raw consumption is massive!
I would also point out that the toxic smoke released during the production of the charcoal in the first place needs to be considered. This is 'invisible' in so much these fumes are released during the raw production phase. Out of sight, out of mind. Propane burns 'cleanest' (but this is over balanced by the much larger production of C02 per working hour - see article referenced above )
There is a reason why Europe was pretty much de-forested during Medieval times. Charcoal can be made any place you have trees, but the consumption rate is extreme, and you can cut and burn far faster than you can grow replacement trees. They did not start using coal, with all its source and transport problems, until they had pretty much cut all the trees down.
* One of these is NORSEFOLK, which is in at least it's third rendition (as the flakes overcome and drive out the serious). People were talking about black fabric, coloured sheep and dyes. And making a bit of a mess of it, frankly. I had made a comment about historic concepts being different than modern ones. I used two specific examples : The Greek references to 'wine dark sea' - and traditional blacksmithing references to 'red heat'. Two separate responses are blended and edited for use here.
1 comment:
Thank you for posting this stuff for the rest of us. I'd not compared the fuels, and chose charcoal simply because I can make it for little more than the labor.
Post a Comment