I'm trying to set up the next person in the series. Might be a bit delayed considering the time of year!
I really did not get much of a chance to wax poetic about bladesmithing, so in the mean time, I thought I would shove in some past pieces with short comments. Mainly trying to use work that illustrate specific concepts or lessons.
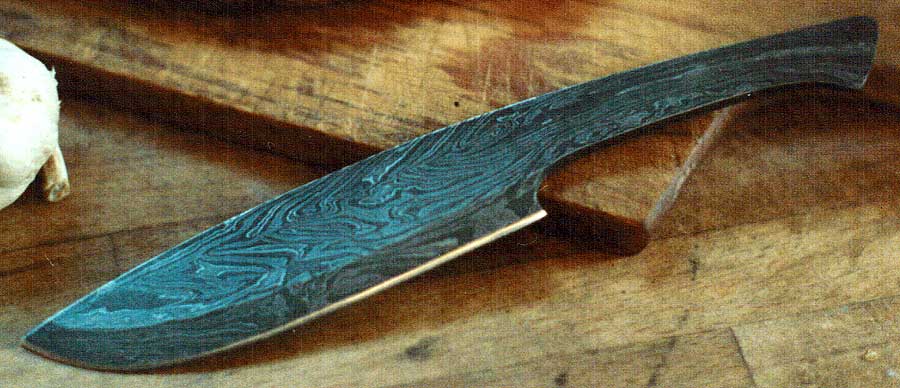
http://www.warehamforge.ca/KNIVES/kitchenknife1.jpg
Kitchen Knife - 1996 (about 11 inches overall)
About 225 layers, mild / wrought iron / 1095
I have always been most interested in the variations in patterning caused by the effect of the hand hammer on a layered steel billet. Creating random, rather than the regular and geometric, lines. My deep interest in Nordic artifact and design aside, the twisted diagonals of multiple core rods create lines that I find most desirable. (I certainly do appreciate the degree of control and precision required in Middle Eastern styles, they just do not appeal to me aesthetically.)
Years back, I had seen some artifact samples of one piece kitchen knives from Roman England in the collection of the Royal Ontario Museum in Toronto. Add to this that I am not that interested in the jewellery like work demanded by ornamental hilting. I consider a good functional knife should have a heavy weight tang, which means covering over a big chunk of layered materials.
Put all these design concepts together, and what resulted was a series of one piece knives, many intended as heavy kitchen knives.
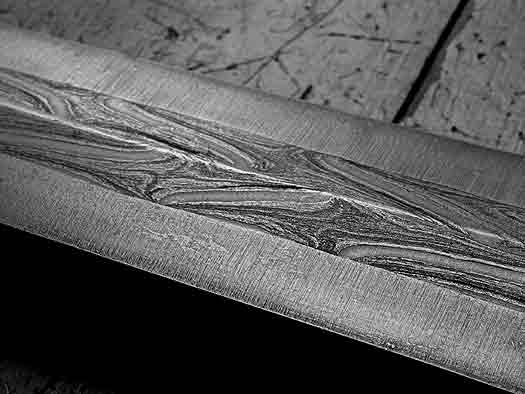
http://www.warehamforge.ca/KNIVES/SwordofHeroes/sword-close-2.jpg
'Sword of Heroes' - 2000 (22 inch blade)
Two nine layer cores with spring steel edges
Hilt is forged steel guard, moose antler, with cast in place pewter pommel weight.
(Yes, those are welding flaws to those looking closely!)
I had been making a lot of pattern welded knives into the 1980's and 90's - with good success with the welds. In arrogance, I thought I was able to move to sword sized lengths. To double the presumption, I accepted a commission for a 2/3 scale version of the Sutton Hoo sword. (eight *complex* twisted cores with 150 layer edges)
Wrong, wrong, and wrong.
Six weeks of work to the quench. A sharp crack.
I ended up with an eight inch knife.
Oh - by the way:
Don't attempt to do long complex welds in an unheated shop - in what turned out to be the coldest winter here in 150 years...
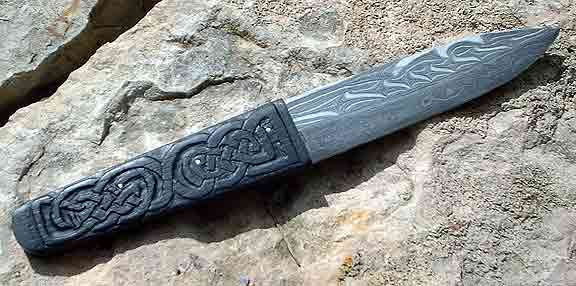
http://www.warehamforge.ca/KNIVES/knives07/ramsayR.jpg
'Wedding Sgin Dubh' - 2006 (5 1/2 inch blade)
About 260 layers of mild / L6 / wrought iron / 1095
Handle of bog oak (2000 year old Roman dock from London)
Layered steels certainly look great, but straight carbon steel will give a much better *working* edge. My personal approach is to make the back half of the blade of twisted rods, and the edge side of two layered slabs with a solid carbon steel core. The two separate pieces then are welded together to make the starting billet. This maybe adds an extra step, but I think gives a better *functioning* blade.

http://www.warehamforge.ca/temp/hectors-mark.jpg
'Hectors Bane' - 2012 (about 11 inches)
Bloom iron with spring steel core
I know I have been strongly influenced by the work and concepts of Lee Sauder. A bit of the similarity of approach may also lie with our shared feeling about to the whole 'art and mystery' of bloomery iron.
I also think that the raw and fractured edges of a parent bloom are an important part of the intrinsic nature of the material.
I have far more raw blooms than consolidated billets, fewer still are the billets that have been worked into objects. Most of the completed objects so far have been simple historic based pieces.
I am quite torn right now on this - how best to utilize my iron blooms. Refining this material, so massively difficult to create, down to perfectly consistent working bars, seems pointless to me (Sorry to some of my research partners and friends reading). The intrinsic quality of bloomery iron is hidden in that perfection.
Sad truth is that within blacksmithing overall, the single best way to turn the effort of all our work is through creating highly ornamented knives. I'm still struggling with all this - the best way to turn the unique qualities of bloomery iron into decorative objects that can both reflect their unique origin, but also command the $$ value that would attempt to provide for all that specialized work.
I hope everyone, with all our different personal paths, are able to finally put up the hammer for a couple of days, and sit back with a beverage of choice. Try to reflect on just how much you have actually *done*, not just the long list of what still remains to be tackled. (And boy, I wish I could be better at taking my *own* advice!)
No comments:
Post a Comment