What I haven't seen though is any talk about the internal pressure of the furnace and what effect it has on a bloom. I was thinking of modifying one of the Rockbridge furnaces to increase the internal pressure as a way of increasing the temperature.
Has anyone tried doing this? If so, was it helpful? Hurtful? Aside from a different way to regulate temperature, I'm speculating that the rate of reactions inside the furnace would increase at a higher pressure, so I wanted to try it to get a better yield.
Byan
(link to complete thread)
My team here has made some input pressure readings. Honestly using fairly cobbled together instruments. This primarily to counter criticisms (largely from theoretical academic commentators) that all the current work is not 'scientifically rigorous' enough.
(But like Lee Sauder says : 'If you don't get any iron - whatever you have done *has* to be wrong'.)
The first thing we tried (cheap and only a relative measure) was a simple U tube with water in it attached to the tuyere side. This gave us some rough ideas - at least between individual smelts.
Eventually I got a small guage (off E-bay) that measured 0 - 30 psi range. (The trouble I had was finding something in the right range, at a price I could manage.)
Some of the individual smelts in our series here have the input pressures measured. You would have to check through the individual 'smelt data' records one by one - there is no centralized table with all the variables charted from all the experiments. (Neil and I am working on that however - with plus 60 smelts, and so many measurement points, its pretty ugly.)
Overall, the average we recorded for input pressure at the tuyere was 3 - 5 PSI.*
We also were using a rough guage for input volume. This consisted (budget again) of a wind surfer's speed guage placed across the input pipe. The volumes were calculated mathmaticaly from the flow speed. Again not the ideal, and it turned out fatigue in the vanes at the high speeds measured really effected instrument performance with time.
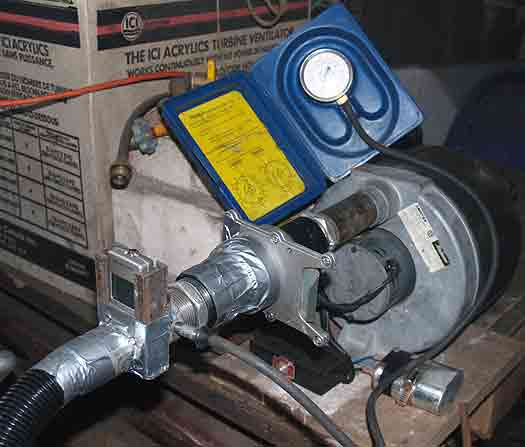
I have been using a different method than Lee uses for controlling the input air from the electric blower. (I've managed to purchase one of the same high end blowers he uses by the way). You can see the sliding plate gate (from a dust collection system) located just at the exit from the blower. So I'm limiting the amount of air into the entire downstream system. (Lee uses a moveable plate just in front of the tuyere set up, venting off excess air.) Both of us have some rough calibrations on these valves that let us have some rough approximation of the air we are providing to the overall system. Mine is marked (very rough approximations!) of 100's of litres / minute (based on earlier measurements). Lee's (was) marked in fractions of total possible (1/4 - 1/2 ...)
My smelting partner, Neil Peterson, is driving an experimental series investigating Viking Age glass bead making furnaces. (Even *less* archaeology than for iron smelting furnaces!). He has deeper pockets than I certainly do (!) and has recently invested in a multi input data recorder system. Along with high temperature probes, he has purchased some modules that will record pressure, and a better quality vane type air speed (so volume) instrument. We still have to assemble the fittings and run some tests, but we have good hopes for better (more consistent) measurements into the future.
You may have gathered from all that - my thrust here has been to researching possible historic *process* - with less concentration on *product*.
I have to agree with what Mark Green has said : That historic air delivery systems may not result in the most efficient utilization of ore = not the best quality blooms. You most certainly can *make* iron in lower air systems (and this most certainly was the method for much of human made iron production). What many researchers miss is the second stage - of bloom to bar. What you may gain in simplicity from ore to bloom is competely lost by the extra labour / materials converting a lacy bloom into a working bar.
Lee has much better experience / notes / observations about this aspect.
Ok
Lee and Skip experimented and documented and then introduced to all the concept of high volume air = better ore to bloom conversion, both in terms of size and density. (Historic note, look at the impact of water powered systems circa 800 - 1100 AD in Europe - pretty much the same thing!)
Although some experimenters have produced measurements of input air pressures, I am uncertain that anyone has attempted to measure pressures inside the actual furnace itself.
As Mark as mentioned, delivery air needs to be considered in terms of not only *volume* but also in terms of *pressure*.
This is why people attempting to use rotory blacksmith's forge blowers as air sources often have less than the best results. Those equipments produce a large volume - but at virtually no pressure. The air simply does not penetrate through the tuyere diameter into the charcoal mass. Increasing the diameter of the tuyere might assist this. Using multiple tuyeres would certainly help (and both methods are seen in historic systems.)
But in actual fact, none of us need to really worry so much about absolute pressure measurements, or even with measuring air volume. The best 'working' measurement is via charcoal consumption. Rate of charcoal consumption is also the effect of internal temperature and size of the effective heat zone. Bigger and hotter = faster charcoal burning.
Most of us are working on some variation of the 'Sauder System', what historically I would call the 'short shaft' furnace. Most typically our working furnaces have an internal diameter of closer to 10 - 12 inches.
This is quite important when discussing measurements and working methods.
As you have seen, there is a dance between ore / charcoal / furnace / air. My own experience is that there is no *absolute* 'perfect' furnace. Any basic design will have to be modified based on changes to those four primary elements. Hematite will not produce the same results, even in identical furnaces and method, as the bog iron ore analog I typically use here.
I'm (educated?) guessing that any attempt to modify the internal gas pressure in what is a very rough and simple furnace will prove far more effort than effective in result.
Past experience has proved the simplest way to effect the reaction ability of a furnace is just to increase the total stack height. (Nice example there, Mark gave 40 inches as his ideal stack height - I usually build for closer to 24 - 30 inches. My standard furnace diameter is larger, rarely below 10 inches, to his reported 8 inch minimum. I know we are working with quite different ore types, and maybe charcoal as well.)
There are just too many other variables for a 'one size fits all' design. (So many things that can, and often do, go wrong!)
No comments:
Post a Comment