This posting a bit out of current order, coming from the iron smelting event at the Museum of Ancient Mazovian Metallurgy, Pruszkow Poland, Sept 7 - 12, 2016.
Second Iron Smelt
Sunday Sept 11
I had hopes of re-using the upper portions of the furnace from the
first smelt, which despite having been lifted off to expose the bloom, was still in
fairly good condition.
Well...
I had told event organizer
Kamilia Brodowska that for the second smelt, I would be happy to work with a group of three younger volunteers who where keen to take part.
Ok, 14 years old, semi keen, proved not used to actual hard work, but all in all they did stick it out for two days and eventually sorted out into tasks that suited their abilities and interests.
Early on build day (Saturday), while starting to mix clay, one of the lads tripped up (somehow) and fell on the existing furnace.
Guess what boys? This means you get to experience mixing even * more * clay, then building an entire new furnace!
 |
Furnace 2 - during pre-heat Sunday morning. |
I decided to build this furnace raised on a plinth. In this case made of the raw clay brick that had been supplied in large amounts for the various builds.
Unlike the first furnace, this one was slightly tapered towards the top. With 22 cm internal diameter at the top and about 30 cm at the base.
It had a wider tap / extraction arch than number one, at 28 wide by 20 cm tall.
Typical height, at 54 cm above tuyere.
Again the copper tuyere, set 5 cm proud of the interior wall, roughly 20 degrees down.
Charcoal fines base set at about 15 cm below tuyere centre.
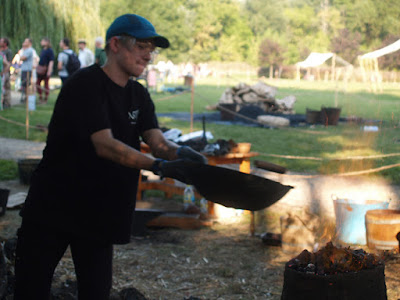 |
One of the boys on Charcoal |
Ore used was the Harres from Denmark (thanks to
Niessen & Olessen), total 41 kg.
It took the two boys working Charcoal and Ore to get a co-ordinated addition system sorted out, but once they had it figured they did a very good job. (The third member proved very good at public interface, so he undertood explaining - in Polish - to the many people watching.)
I used a method that had been illustrated by
Micheal Niessen, earlier during his first smelt.
Micheal makes his first charges not of ore, but of 2 - 4 kg of iron rich tap slag. He suggests that doing this will create the needed slag bowl at the bottom of the furnace much faster. This in turn means that metallic particles being reduced will start too collect sooner, with the end result of more effective bloom production. Both his direct experience and our use of this method at the workshop certainly prove this to be the case.
 |
Bloom from smelt two |
The end result was an extremely nice 8.2 soft iron bloom.
This would prove one of the largest created, out of a total of some 15 + individual smelt attempts by the various teams. Most certainly this bloom showed the single best return, with a yield of 20%.
Again, on comparison with the Norse artifact bloom, you can see the shapping is almost identical.
(On a suggestion by
Lee Sauder, we intentionally left the cut to about the same depth to illustrate this.)
Plans are to add this specific bloom to the Museum's display as a sample of what historic blooms would have looked like!
Great work by all.