"Ancient beads were often made on cast iron tapered rods, without the use of a separating agent. Once a bead was finished, the rod was heated to red-hot and plunged into a container of salt. This created a chemical reaction, causing the cast iron to rust and the bead could be easily tapped off the rod."
Quote from www.timelessbeads.net/islamic_folded.htm
(Note: In all fairness to Jhan, her interest lies in duplication of historic beads using modern flame working tools and methods. She clearly references that someone else told her this, so I am not critical of her otherwise quite good web site!)
First, what is being referred to here are artifact wrought iron mandrils. Two have been found in the Viking Age layers at Ribe, Denmark. (This is the focus of interest of Neil Peterson's experiments with DARC.)
As an experienced metal worker, I do want to stress the actual material. There is a significant difference, both chemically and structurally, between the various different iron based metals that might have been used. This also extends significantly to the oxidation rates.
I know that 'cast' iron was not used historically. This high carbon alloy was not clearly understood or widely employed for any purposes until into late Renaissance times (varies depending on location, much earlier in the East).
Most likely is some form of bloomery or wrought iron, the low carbon material most commonly used for all forged objects up till the Industrial age.
For comparison, modern mandrills are typically a nickel alloy (stainless) which basically did not exist until fairly recently (the Modern Age - say 1900). This material is used because of its great *resistance* to oxidation.
I have made up one actual 'wrought iron' mandrill, using antique recycled metal (on a guess from the late 1800's). This specific material most closely matches the bloomery iron that would have been available during the Viking Age. The form is (loosely) based on one of the artifacts from Ribe. The shaft is about 30 cm lng and is mounted into a wooden handle. The fairly heavy cylindrical body shoulders in near the tip for about the last 3 - cm. The diameter here is roughly 3 mm, tapering slightly to the end. To date we have primarily been using a fairly standard method of coating the working area with a clay resist.
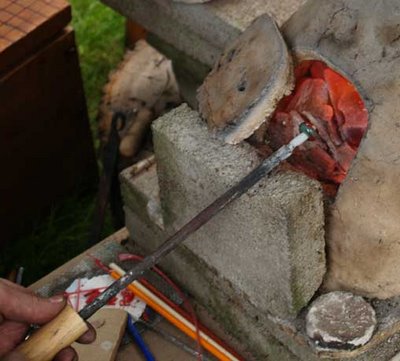
I have reservations that the theoretical salt water quench method as described would actually work in practice. There are two primary forms of iron oxide in play here. Chemically these are Fe3O4 or Fe2O3:
The first (Fe3O4) is the high temperature form - black oxide or fire scale. It is hard, brittle, and adheres both tightly and strongly to the parent metal. Its formation is fast - due to the temperatures (above about 450 C or so). I just can not see this being of any value to the bead making process, as the glass strongly attaches to this layer, then due to the bond between the oxide and the metal, it remains firmly in place.
The second (Fe2O3) is the low temperature form - red oxide or rust. This layer is soft and crumbly, and breaks away easily under any mechanical pressure. Generally this is a slower formation, taking place at room temperatures. This process is accelerated (ask the chemists why) by water, and a bit more so by salt water. Now, it might be possible to use this layer as resist, as it does easily break free from the parent metal. This layer is certainly extremely thin. This presents two problems. First - there is not much separation layer to begin with, so it would be extremely easy to scrape it completely off and expose the metal underneath. Second - the layer is so thin that it conforms closely to the shape of the parent bar. The interior of the glass wraps tightly around any irregularities in the metal mandril. Although every attempt is made to produce a mandril with a perfect cylinder, or a slight conical section, one of the functions of a thicker resist layer is to lift the glass away from any imperfections. Such a thin layer as the oxide would create would just not give enough gap between metal and glass.
I should mention that one observation I have from forging actual wrought iron is that when it is quenched from incandescent in water, often a thin film of red iron oxide will form on the surface. As suggested, the quality of the iron does effect this. However, given the problem of creating a suitable 'release gap' I still think that this natural oxide layer is just not thick enough. Even with the slight acceleration produced though the use of salt water, the layer of Fe2O3 created would far to thin to be significantly useful here.
I suspect that this whole idea was theoretically reverse engineered to explain observations of a special situation. I believe (?) some glass beads were found to have a very thin layer of iron oxide in the interiors of the holes. How to explain this? Pair this observation with the discovery of a couple of wrought iron mandrils. Presto! A working method, now enshrined in the literature (although never actually tested). Repeat that WAG, until it has become an accepted method (still not tested).
An alternative : given the wide availability of various iron oxides as ochre deposits, perhaps a well known resist material was simple red ochre mixed with water as a paste. This applied just as we do our fine clay. This is a method that would be easy to test experimentally.
Additional tests:
- As Neil Peterson has mentioned, examine only BROKEN artifact bead fragments from production sites to check for the presence of resist. We know that the thin clay layer is fragile, and relatively quickly will clean away from the interior of any bead actually worn on a string. This does tell us beads found removed from production sites may not yield useful information.
- We tend to take a very long time to make a single bead. Historic production work is sure to be much faster. The way the clay interfaces to the glass is sure to be time dependent. Is there any way to check on this?
No comments:
Post a Comment