I had said in the last entry on this topic set that the pattern is a result of the differing alloy contents of the individual layers in a stack. This is primarily differences in carbon content - so differing hardness.
Right off the start, if you chose certain metals, there may also be a difference not only in chemistry, but also in texture. Wrought or bloomery iron is different not only because of relative carbon content, but also because of the microscopic inclusions of glassy slag. 'Better' wrought iron has less of these inclusions, but the material can vary widely in consistency, even within the same bar. Bloomery iron not only has the same range of slag inclusions, it also will vary in carbon content within a single bloom mass. (Again, there is a lot of material on all this stuff on both here on the blog and the Wareham Forge web site.)

Remember that ALL iron metals from the Viking Age would be only bloomery produced. So all have some measure of slag included. Carbon content will also vary considerably. Carbon content is the primary alloy component that determines relative hardness of individual iron metals. The result here is a blade material from this period which can be called 'steel' (iron plus carbon) but is in fact quite different in texture than modern steels. (Correctly called 'bloomery steel' ??)
In modern layered steel making, the smith will pick various alloys - and often production types, to create the maximum differences between the finished layers. Typical choices are:
- Antique Wrought Iron - considerable variation between individual pieces, quite low carbon (often virtually none), slag inclusions - very soft, produces a rope like texture on etching.
Mild Steel - extremely consistent, lower carbon content (1/5 C % typical) - medium soft, produces an even light grey colour on etching
Spring Steel - extremely consistent, but many exact contents available (1/2 % C typical) - medium hard, produces an even medium grey on etching
Tool Steel - extremely consistent, but many exact contents available (1 % C typical) - very hard, produces an even dark grey on etching
Nickel Alloys - extremely consistent, but many exact contents available, both in terms of exact mixture and also carbon contents ('L6', which is 1/2 % C and 0.5 Nickel is common) - medium hard, produces bright silver lines on etching.

Note that the exact effect of the etching process depends to a very significant degree to the exact etching solution chosen. (On my modern work, I use two, Nitric for cutting, Ferric Chloride for colouring.) Viking Age process is limited to vinegars as actual acids, with possible use of salt water or urine more for colouring (controlled corrosion).
So right off the top, you can see that the exact choice of metals will significantly effect the relative hardness of the individual layers, thus the way that polishing would effect a layered billet, even before etching. Note that the exact way the layered block is handled (the annealing / hardening sequence) will also effect just what results polishing may have.
Of course, in the Viking Age, the exact choice of alloys chosen would be more limited than the list above. Right off the top, the only way to employ nickel based alloys historically would be through the use of meteor iron. (High nickel contents of 7 - 15 %, no carbon at all.) This may not be as large a stretch as it might at surface appear, I have seen one study (Museum of London) which suggests a good number of blades (at least in their collection, 1066 - 1400, as high as 10%) show traces of nickel content.
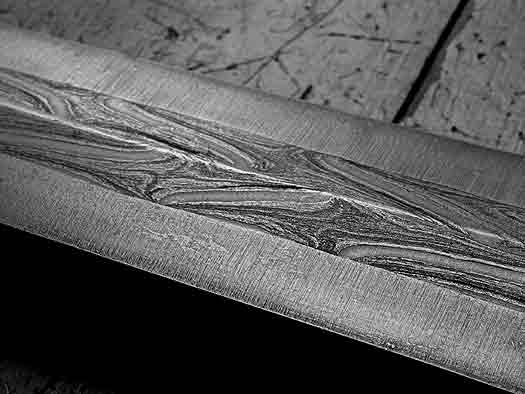
Generally however, it may be safe to say that the range of carbon contents for actual VA artifact blades is not going to be as wide as that used by modern bladesmiths. Historic blades will not be able to utilize metals that create texture differences. Although use of nickel alloys is possible, it is more likely to be unusual. All of this is going to result in less dramatic results on those artifact blades.
there is a part four to this, Carbon Migration
2 comments:
To obtain native nickel to high percentage , meteorite was the one and ONLY possibility, but you're forgetting one thing though: people in the viking age experimented alot and reduced various ores, plus the baltic region was and is still one of the places where nickel ore is very abundant. The ancient chinese reduced nickel rich ore -namely cupronickel ore- and (they also did the same for chrome rich ore), and relatively pure nickel can be easily seperated from copper by various low-tech methods .
It wouldn't be "historically inaccurate" to have vikings use nickel ore(even if they probably didn't, it was possible) and not only meteorite for the following reasons:
-various nickel ores are present in scandinavia in sufficient quantity
-vikings had commercial ties with asia and it is historically proven (hoards in Scandincavia containing buddhic articfacts in gold), hence they could have purchased some cupronickel or some nickel from asia.
It's period correct to use reduced nickel or cupronickel for the viking age(it was POSSIBLE at that time, but either some have tried and the proof disappeared, or it never happened), but it's historically wrong , go figure! Probably they didn't botehr since meteorite was available and it greater quatity than in more temperate regions.
'Mjod'
Please take as given that trace elements in the starting ore are 'generally' passed along to the resulting bloom iron.
However, from what I have read, meteoric iron has nickel contents ranging from 5, 7, even as high as 15 %. In comparison, modern stainless alloys are in the .5 - 2% ranges. The marker of such high nickel contents in ancient or historic objects is a sure signature of the use of meteorite material.
Post a Comment