At the Heltborg symposium, metallurgist Arne Espelund stressed several times that he considered measurements of the slags produced during an iron smelt to be be critical to evaluating the process. We rarely actually do this, as the raw mechanics (and general chaos) of an experimental smelt in the field make exact measurements difficult, if not totally impossible.
That being said, I was presented with a unique opportunity with the last smelt here in Wareham. This smelt was inside our standard clay cobb 'Norse short shaft' style smelter, and was a full scale test of the 'DARC Dirt 1' bog ore analog material. (See Monday's entry)
In brief:
Charcoal consumption - average of 10 minutes per 1.85 +/- kg
Air rate - 90 - 95 KpH = 750 - 800 LpM
Ore charges - roughly 1 : 1 to charcoal (2 kg per charcoal bucket)
Total ore added - 20 kg
This then represents most of the input numbers. The most important is the total ore addition. This needs to be modified by the water content of the ore. That was determined by taking a 500 gm sample and baking it in a propane gas forge at roughly 950 C (by colour) for about 10 minutes. The sample was then again weighed - the result was a net loss of 47 gms, or the sample being roughly 10% water.
The ore analog itself is made up of a mix of 80% 'Spanish Red' iron oxide, combined with 10 % silica sand and 10% flour. The Spanish Red itself is roughly 96.5 % Fe2O3 with 2 % SiO2 (no data on the balance)
So of the 20 kg ore added, 2 kg was water, leaving 18 kg remaining.
Of that 18 kg, a further 1.8 kg was the ( inert ) flour, leaving 16.2 kg material.
Of this, 15.6 kg is the iron oxide, and there is .3 kg of silica.
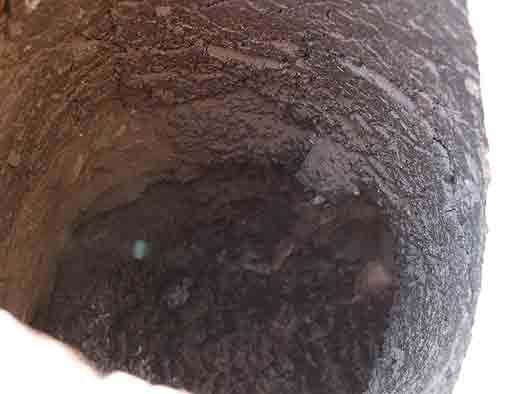
Now this smelt was quite unusual, in that there was extremely little effect on the structure of the smelter itself. The image above shows the inside surface of the smelter, with the area around the tuyere in the upper right.
First, there is very little erosion of the wall material. The area above the tuyere, normally sustains damage, but in this case you can see that the wall has hardly been effected. Curiously, what erosion that took place was just bellow the tuyere. The tuyere itself was also only slightly effected, and other than a slight rounding of the square tip, still remains the same distance proud of the wall surface as at the start of the smelt.
Second, very little material, either slag or partially sintered ore, can be seen remaining attached to the inner wall surface. In many past smelts, a considerable build up of these two materials can be seen.
As this was a newly constructed furnace, it proved possible to gather, sort and record the various slag types produced over the smelting process. The furnace was constructed on a relatively clean base of course sand, allowing any related debris to be easily distinguished. After the smelt, the largest pieces were gathered, and sorted by eye into types. All the remaining debris, including ash and unburned charcoal, where then passed through a 3/16 inch (about 4 mm) screen. Next a magnet was passed through the remainder, extracting any pieces containing enough iron to allow attraction. These were measured separately. The remaining larger pieces were then sorted by eye, using the same skills used to daily clean clinker from my forge fires. Any pieces of slag much larger than about 1.5 cm were sorted by type. (So there will be some loss of smaller particles)
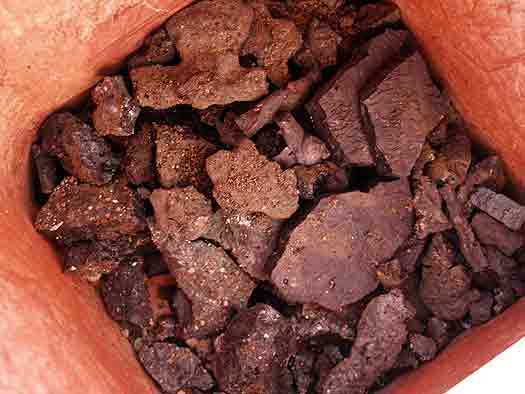
This smelt had a major 'self tapping' event occur late in the sequence, during the last stages of the burn down phase. This slag was fluid, dark olive / black and proved to have no magnetic quality.
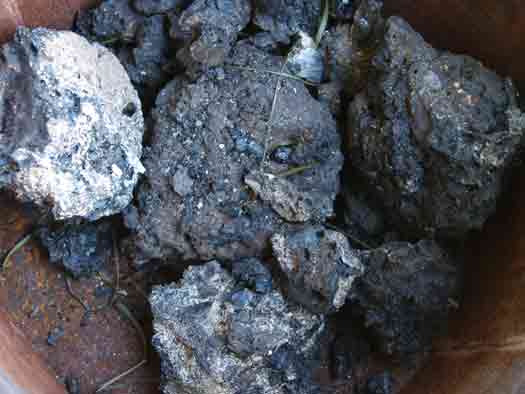
As the bloom was extracted, a mass of hard slag remained attached. This material (we call 'mother') cools much more quickly than the iron bloom. It is also brittle, and is shattered off the bloom under the effect of hammering on a wooden stub during the initial consolidation step. Generally this material is quite dense, and a medium matte grey in colour. Some portions of it may prove magnetic (fragments broken off the bloom). Most of the pieces are walnut to fist sized. As this work station is a grassed area just to the side of the smelter platform, any fragments smaller than about 3 cm were surely not recovered.
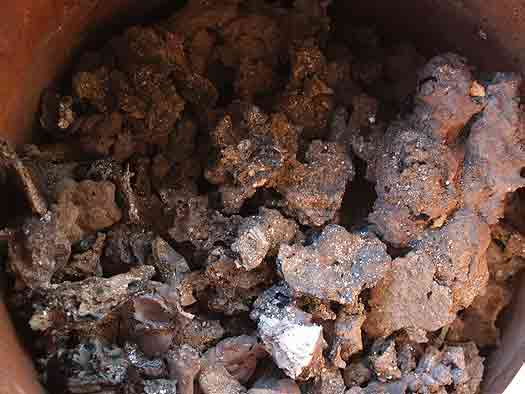
Considerable slag material remained both inside and scattered around the smelter after the bottom extraction of the bloom through the tap arch. This material would have formed the bulk of the slag bowl. These pieces are also a dull medium grey, and often include some imbedded charcoal and ash. Generally the pieces are quite irregular and range around 'walnut' sized.
The total weights of the collected slags:
Magnetic 'Gromps' - .5 kg
Tap slag - 3.2 kg
'Mother' - 2.3 kg
Bowl pieces - 6.6 kg
TOTAL COLLECTED - 12.6 kg
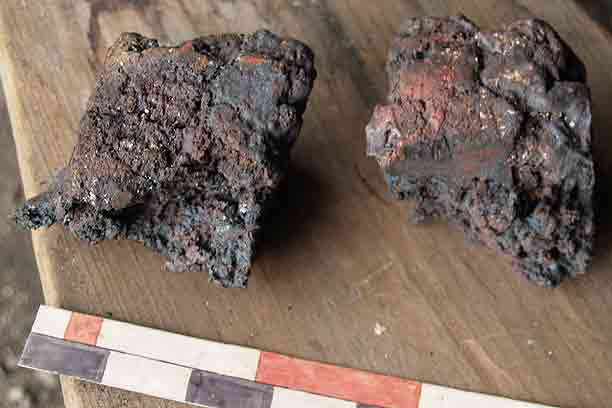
The bloom itself for this experiment is somewhat smaller than our usual. One factor here is that the weight was taken at a later step in the consolidation process than what is normally the case. (Standard practice is to make a single consolidation heat, striking off the majority of slag 'mother'. In this case, the bloom was subjected to two additional heat / hammer sequences.) The bloom reacted well to hammering, but was somewhat 'lumpy' in texture. Through spark testing, it appears to have some low carbon content (roughly equal to a mild steel).
Weight of Bloom - 1.9 kg
TOTAL INPUT - 16.2 KG (oxide 15.6 / silica .3)
TOTAL OUTPUT - 15.5 kg (slag 12.6 / bloom 1.9)
This looks pretty close to matching, assuming a reasonable amount of slag material lost in collection and the rough sorting process used.
1 comment:
Would there be any real need to assay the slag or the bloom?
I guess, the question might be better asked...would there be any need to pay the cost of an assay.
Bill
Post a Comment